比斯特的BT-2113B-18/21電池組半自動生產線的工作流程是一個高度集成且精細的過程。從電芯的初步放置開始,每一步都經過精心設計和嚴格測試。生產線上的自動化設備能夠精確處理電芯,完成包括自動上料、自動面墊、電壓內阻分選、自動分檔、儲存、自動入盒、正負極CCD檢測和自動點焊等一系列操作。這不僅提高了生產效率,還確保了每個電池組的一致性和可靠性。本文將詳細解析BT-2113B-18/21電池組半自動生產線的工作流程,展示從電芯上料到電池組性能測試的每一個環節。
一、自動上料
首先,電芯的上料是生產流程的基礎。在BT-2113B-18/21電池組半自動生產線上,工人將裝滿電芯的盒子放在傳送帶上,傳送帶自動運作,機械手夾取電芯到下一部位,空盒子通過另一側輸送帶運出。這一步提高了自動化程度,降低了工人的勞動強度。
二、自動面墊
接下來是自動面墊環節。該生產線適用于18650和21700電芯,自動貼圓形青稞紙以增強電芯正極的絕緣性能,提高電池組安全性。這一功能可關閉,用戶可根據需求選擇是否貼紙,提高了生產線的靈活性并降低了成本。
三、自動分選
隨后,生產線進入電壓和內阻的自動分選階段。借助高精度傳感器,設備自動測量每個電芯的電壓和內阻,并據此將其分類到不同的檔位。BT-2113B-18/21生產線設有五個分選通道,這一環節對確保電池組的一致性和穩定性至關重要。此外,設備還預留了掃碼位置,以便未來增加掃碼功能,從而實現對電芯信息的多方位追蹤和管理,進一步提高生產效率和產品質量。
四、自動儲存和入盒
電壓和內阻分選完成后,電芯進入儲存階段,以便更好地進行裝盒。BT-2113B-18/21生產線設有五個裝盒口,自動取出同一檔位的電芯并裝入相應的膠盒中。裝好電芯的膠盒隨后被升降機自動傳送到人工裝支架位置,實現了電芯的自動化整理和傳送,為后續的人工組裝提供了便利。
五、CCD檢測
在人工裝支架之前,生產線還配備了自動CCD檢測正負極的功能。通過高精度的CCD相機和圖像處理算法,設備自動檢測電芯的正負極位置,確保組裝的準確性。合格的電芯繼續送往下一步,不合格的電芯則通過升降臺送出,人工擺正后可繼續進入下一步工序。
六、人工裝支架和模具
然后是人工組裝支架階段。工人在完成模具組裝后,將鎳片放入其中,接著進行自動點焊。點焊系統運用了先進的晶體管技術,實現雙面自動點焊,確保焊接過程快速且精確。通過精確控制焊接時間和電流強度,設備保障了每個焊點的牢固與可靠。這一環節是電池組組裝的關鍵步驟之一,直接影響電池組的質量與性能。
七、電池組綜合性能測試
此外,生產線還提供了電池組性能測試機的選項。用戶通過連接性能測試機,可對組裝完畢的電池組進行多方位檢測,涵蓋電壓、內阻、容量等指標。這一步驟有助于確保出廠電池組符合質量標準,提升客戶滿意度和信任度。
經過一系列精密高效的流程,BT-2113B-18/21電池組半自動生產線產出的是高質量、高性能的電池組產品。從電芯上料到電池組性能測試的每個環節都充分展現了自動化和智能化的優勢,不僅提升了生產效率和產品質量,還減輕了工人的勞動強度,降低了企業的運營成本。隨著新能源產業的持續發展,比斯特的BT-2113B-18/21電池組半自動生產線有望成為眾多電池制造企業的理想設備。如有更多需求,請留下您的聯系方式,深圳比斯特竭誠為您服務!
審核編輯 黃宇
-
電池組
+關注
關注
5文章
321瀏覽量
25718
發布評論請先 登錄
相關推薦
電池自動生產線:智能制造的典范與未來趨勢
電池組半自動生產線:高效、智能的生產解決方案
電池自動生產線:智能制造的典范
18650儲能電池組PACK生產線:高效、智能、可靠
比斯特自動化:引領儲能電池組生產線智能化變革的先鋒
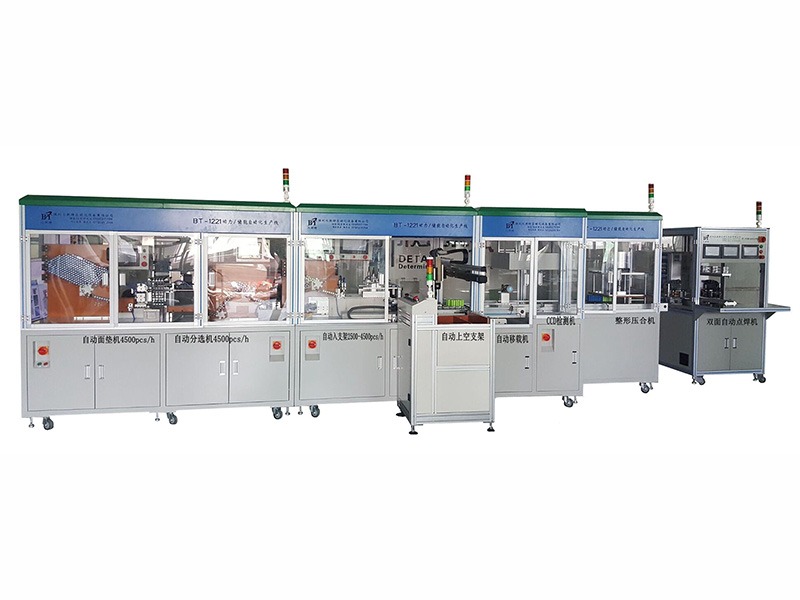
比斯特自動化:引領電池組PACK自動化生產線的創新與發展
智能引領未來:高效電池自動生產線助力綠色能源發展
電池自動生產線:智能化制造的未來趨勢
比斯特自動化|電池組全自動生產線:推動電池制造行業的革新與效率提升
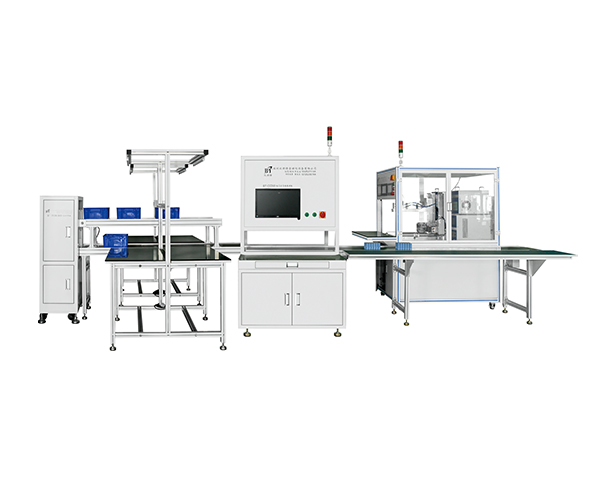
比斯特自動化|電池組PACK自動化生產線:引領能源存儲行業的新篇章
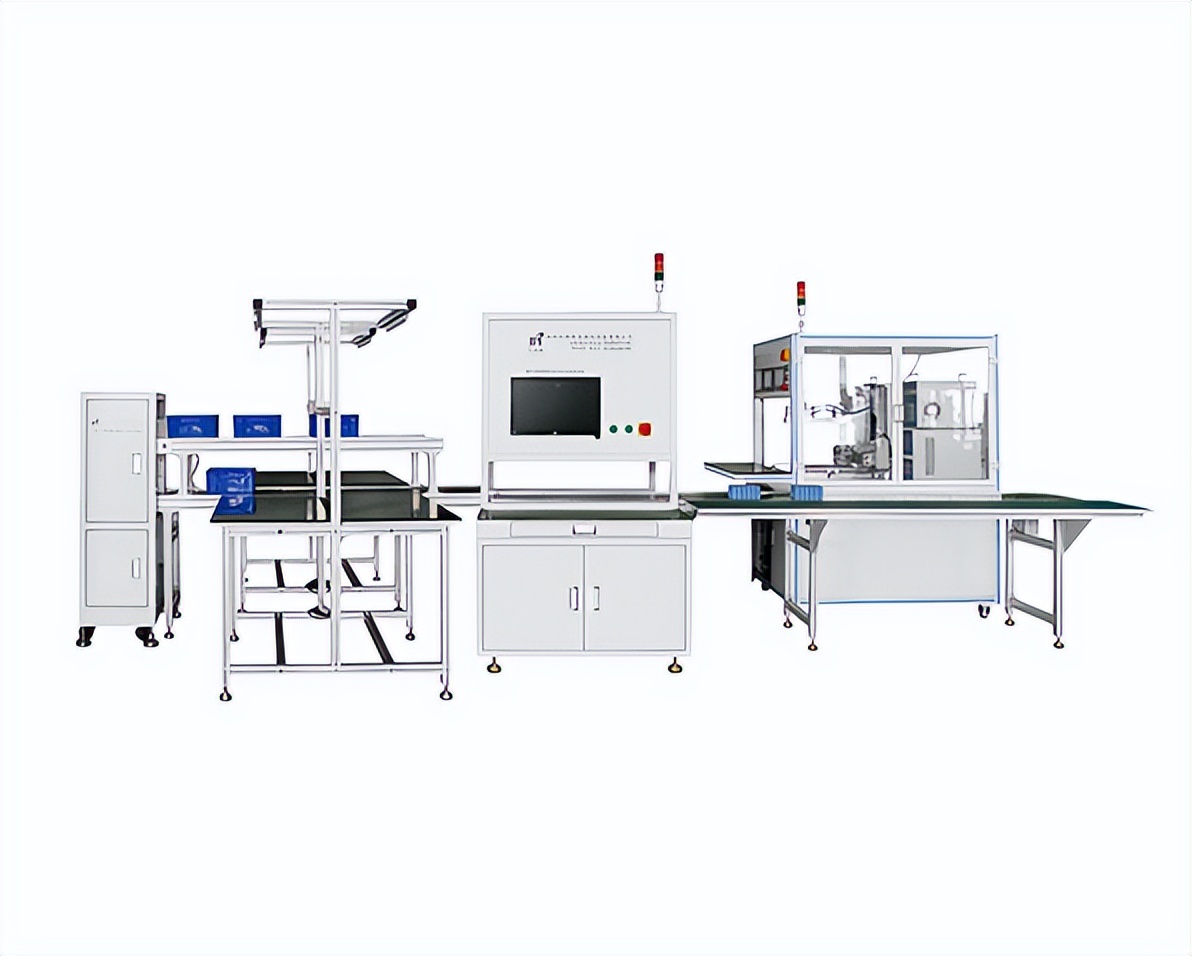
儲能電池組PACK生產線:驅動綠色能源未來的核心
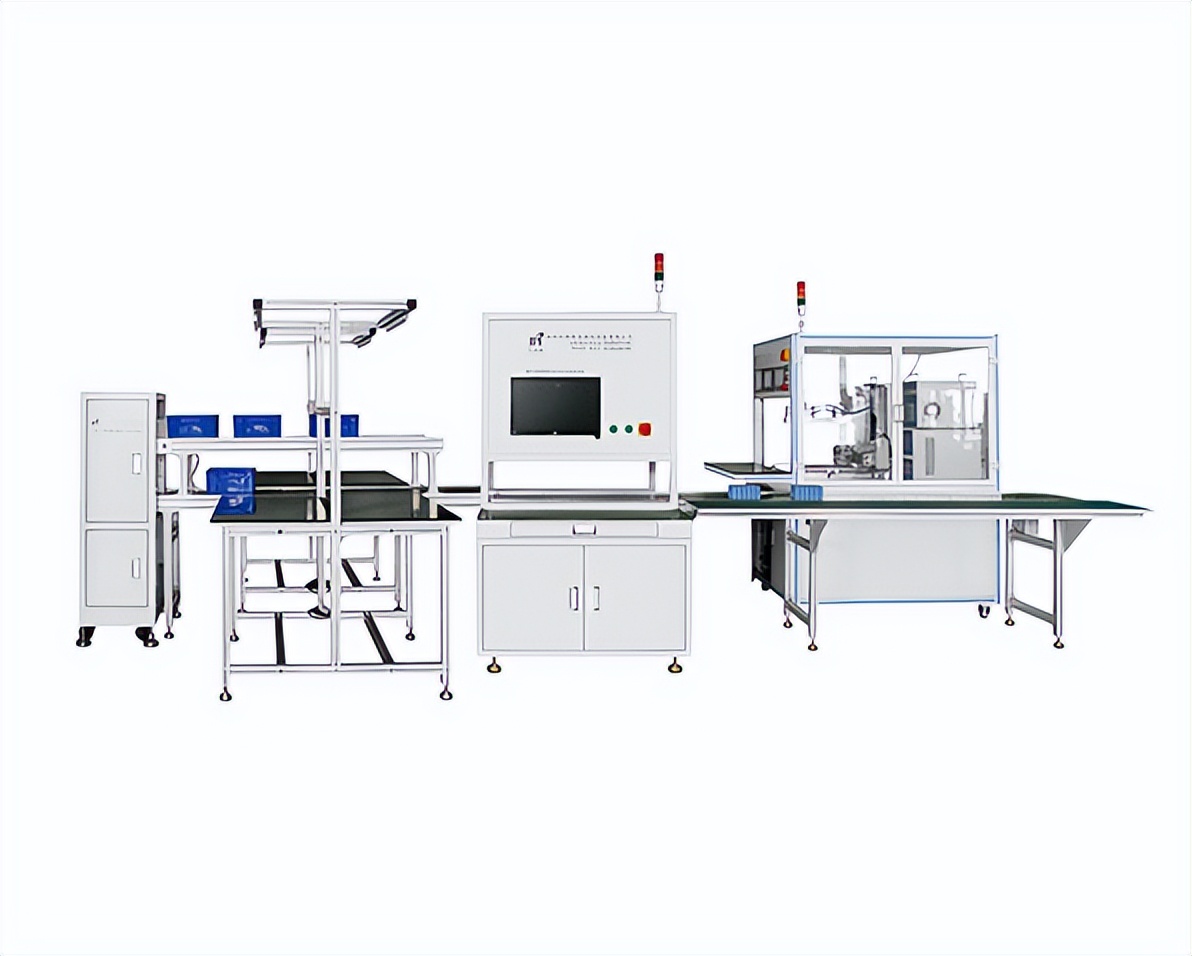
光伏電池片生產線:綠色能源的未來工廠|比斯特自動化
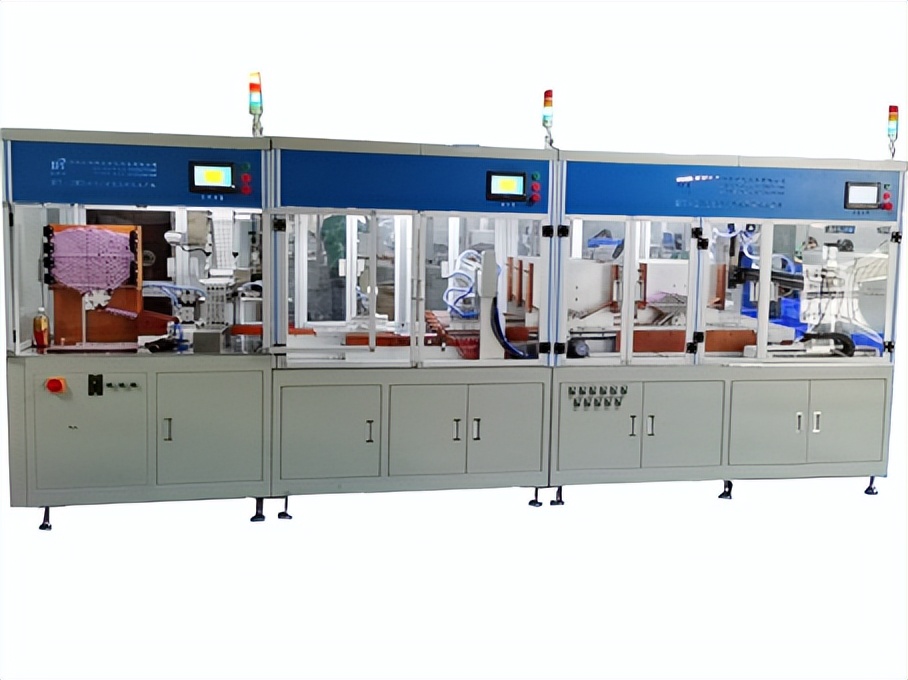
【200個電機驅動】如何快速搭建柔性自動生產線?
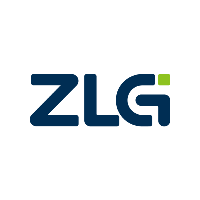
評論