本文簡單介紹了芯片制造的7個前道工藝。
在探索現代科技的微觀奇跡中,芯片制造無疑扮演著核心角色,它不僅是信息技術飛速發展的基石,也是連接數字世界與現實生活的橋梁。本文將帶您深入芯片制造的前道工藝。這一精密而復雜的流程主要包括以下幾個工藝過程:晶圓制造工藝、熱工藝、光刻工藝、刻蝕工藝、離子注入工藝、薄膜淀積工藝、化學機械拋光工藝。
晶圓制造工藝
晶圓制造工藝包括單晶生長、晶片切割和晶圓清洗。 半導體晶圓源自對大體積半導體基材的精確切割,這些基材原本多為具有多晶形態且未經摻雜的本征物質。通過特定的工藝,這些多晶塊被轉化為單晶結構,并經過精確的方向定位及適量的摻雜處理。稱為單晶生長。常用的單晶生長方法主要有直拉法和懸浮區熔法兩種。此過程中主要用到單晶生長設備。 當結晶錠冷卻后,采用適宜工藝對晶體切割產生晶圓片,針對晶圓片表面的損傷和沾污,常采用刻蝕的方式進行處理。常規磨削工藝完成后,硅片表層會遺留一層很薄的表面缺陷,于是需要進一步的拋光處理。目前最廣泛的潘光技術是化學機械拋光技術(CMP),此工藝能有效確保硅片表面實現高度平滑,達到光潔無瑕、宛如鏡面的理想狀態。 最后經過清洗、檢查及包裝后形成用于集成電路設計的晶圓襯底。該過程是一個多重工藝過程,使用到的設備具體包括內圓切割設備和線切割設備、濕法清洗設備、化學機械拋光設備等。晶圓和芯片的加工流程如圖所示。
熱工藝
熱工藝包括熱氧化、擴散和退火。 熱氧化工藝是在硅片表層通過熱過程形成一層均勻的絕緣或掩蔽介質薄膜。這一過程包含兩種主要方法:一是高溫干氧氧化,即在高溫條件下引入純凈的干燥氧氣,促使硅片表面緩慢地生長出結構緊密的二氧化硅薄膜,此薄膜具有較低的固定電荷密度;二是高溫濕氧氧化,該方法利用氫氣與氧氣反應生成的水蒸氣對硅片進行氧化,其氧化速度相較于干氧法顯著提升,適用于生成較厚的二氧化硅層,但所得氧化層的致密度稍遜于干氧氧化所得。 擴散是物質在分子熱運動的驅動下,由高濃度向低濃度流動的一種基本物理現象。擴散摻雜工藝在早期的集成電路工業中占主導地位。通過在硅表面引入高濃度的摻雜劑,通過擴散作用改變硅等半導體襯底材料的導電性。在IC工業的早期,擴散被廣泛用于半導體摻雜。隨著摻雜技術的發展,在高級集成電路晶圓廠中,很少采用擴散工藝進行摻雜。氧化工藝與擴散工藝采用的設備基本一致,一般是立式爐、臥式爐和快速熱處理爐。
光刻工藝
光刻工藝是集成電路芯片制造過程中至關重要且應用廣泛的環節,其核心功能在于將掩模版上的設計圖案精確轉移到襯底表面的光刻膠層,從而形成預設的電路圖案。 依據曝光技術的差異,光刻可被細分為接觸式、鄰近式及投影式三類;而依據對準操作所涉及的面數,它又能被區分為單面與雙面對準光刻;再者,依據光刻膠層厚度的不同,光刻技術還能進一步分為薄膠與厚膠工藝。 一個完整的光刻流程通常包含預處理、涂覆光刻膠(均勻涂覆)、預烘烤、精確對準與曝光、顯影處理以及后烘烤等一系列步驟。這些步驟可以根據實際需求進行靈活調整。 光刻機作為大規模集成電路生產的基石,其重要性不言而喻,是支撐光學與電子工業持續發展的核心裝備。光刻工藝流程如圖所示。
刻蝕工藝
刻蝕技術是用于精確去除未被抗蝕材料遮蓋的部分薄膜區域,以便在薄膜上精確復制抗蝕層上的圖案。 在集成電路制造流程中,首先通過掩模定位、曝光及顯影等步驟,在抗蝕層上形成所需圖案,或直接使用電子束在抗蝕層上繪制圖案。接著,將這些圖案精確轉移至其下方的介質薄膜(例如二氧化硅、多晶硅)或金屬薄膜(例如鋁及其合金)上,構建所需的薄層構造。 刻蝕技術主要分為干法刻蝕與濕法刻蝕兩類。干法刻蝕主要依賴反應氣體與等離子體的相互作用來完成刻蝕;而濕法刻蝕則是利用化學試劑與被刻蝕材料間的化學反應來達成目的。目前,鑒于其高效性,干法刻蝕裝置在集成電路制造中得到了廣泛應用。
離子注入工藝
離子注入技術是目前廣泛應用的摻雜手段,將高能離子束滲透至固體材料表層,從而改變其物理和化學特性。 在半導體材料中注入特定的雜質離子(例如,向硅中植入硼、磷或砷等元素),能有效調節其表面的電導率或構建PN結。與傳統的擴散法相比,離子植入技術具有更低的操作溫度、便于形成淺結、雜質分布易于大面積均勻化以及便于自動化操作等優勢。 如今,離子注入已成為集成電路制造中不可或缺的摻雜步驟,通常由離子注入設備來完成這一工藝。離子注入結構示意圖如圖所示。
薄膜淀積工藝
薄膜淀積工藝主要包括物理氣相淀積和化學氣相淀積。 物理氣相沉積(PVD)技術是在真空條件下,運用物理方法把固態或液態源物質轉化為氣態的原子、分子或離子形式,再借助低壓氣體氛圍(含等離子體)的作用,讓這些氣態粒子在基底上沉積,以形成具備特定功能的薄膜。 PVD技術包含多種具體方法,例如真空蒸發鍍膜技術、濺射鍍膜技術、電弧等離子體鍍膜、離子鍍膜以及分子束外延技術等。時至今日,PVD技術不僅限于制備金屬膜與合金膜,它還廣泛應用于沉積化合物膜、陶瓷薄膜、半導體薄膜及聚合物薄膜等多種類型的材料上。典型的PVD反應系統示意圖如圖所示。
熱蒸鍍示意圖 電子束蒸鍍示意圖 化學氣相沉積(CVD)技術是將構成薄膜元素的氣態或經氣化后的液態反應物,連同必要的氣體輔助劑,導入反應腔內,通過化學反應在基底表面生成薄膜。 這一技術在超大規模集成電路制造中占據核心地位,被廣泛應用于制備諸如二氧化硅膜、氮化鈦膜、非晶硅膜等多種薄膜材料。CVD技術展現出諸多優勢,包括沉積溫度較低、薄膜組分與厚度能精確調控、沉積速率與時間高度正相關、優異的均勻性與重復性、臺階覆蓋率良好以及操作便捷。特別是其低溫沉積能力和出色的臺階覆蓋性,極大促進了超大規模集成電路的制造進程,使之成為集成電路生產中不可或缺的薄膜沉積手段。常用的CVD設備涵蓋常壓CVD系統、低壓CVD裝置以及等離子體輔助CVD設備等。CVD反應系統示意圖如圖所示。
化學機械拋光工藝
化學機械拋光(CMP)技術是集成電路制造中確保全局表面平整度的關鍵步驟,它能生成既光滑又無損傷和雜質污染的表面。 CMP結合了化學與機械的雙重機制:首先,工件表層材料與拋光液中的化學試劑發生反應,形成一層易于剝離的軟化層;隨后,借助拋光液內的磨粒與拋光墊的機械摩擦作用,去除這層軟化物質,暴露出新鮮的工件表面繼續參與化學反應。這一過程在化學與機械效應的不斷交替中,實現工件表面的精細拋光。 隨著光刻技術中透鏡的數值孔徑越來越大導致了曝光視場聚焦深度越來越淺的問題,以及多層金屬互連工藝的廣泛應用,CMP技術應運而生并迅速發展,市場需求也持續增長。CMP設備集成了機械工程、流體力學、材料化學、精密制造以及先進控制軟件等多學科的尖端技術,是集成電路制造設備中技術復雜度高、研發難度大的設備類別之一。
-
芯片制造
+關注
關注
10文章
625瀏覽量
28844 -
晶圓制造
+關注
關注
7文章
280瀏覽量
24109 -
光刻工藝
+關注
關注
1文章
30瀏覽量
1838
原文標題:芯片前道制程工藝
文章出處:【微信號:bdtdsj,微信公眾號:中科院半導體所】歡迎添加關注!文章轉載請注明出處。
發布評論請先 登錄
相關推薦
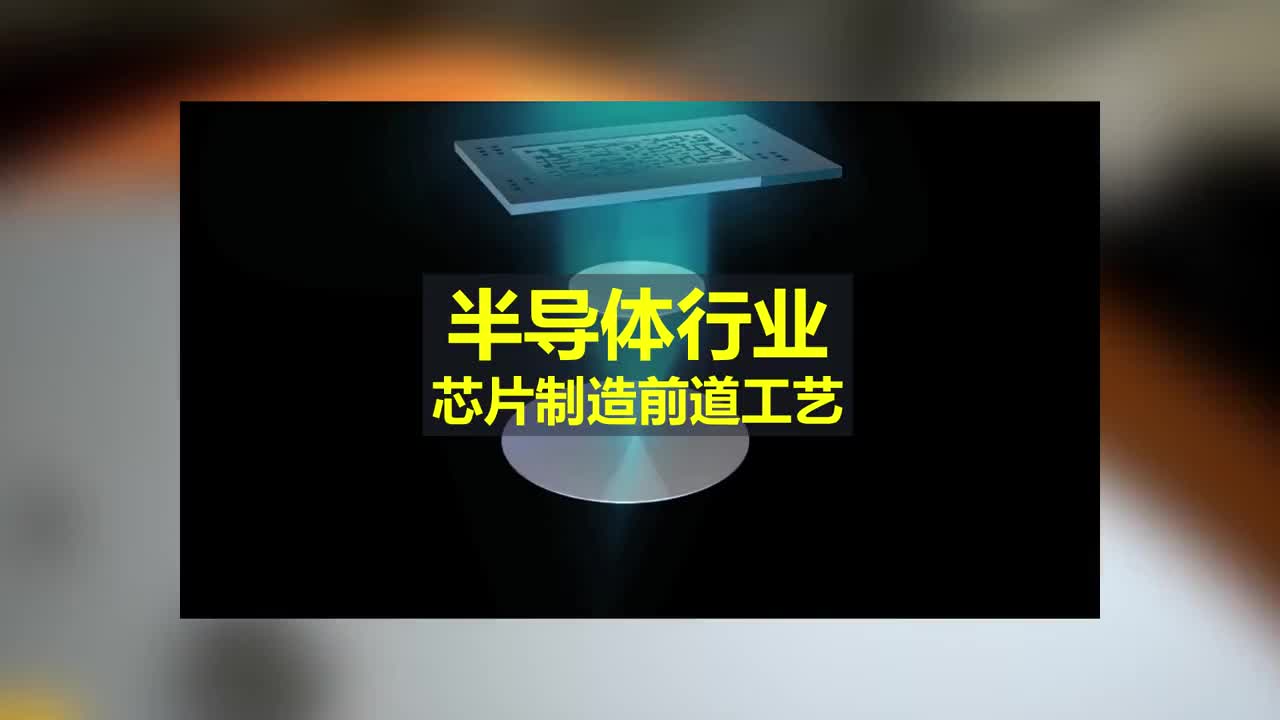
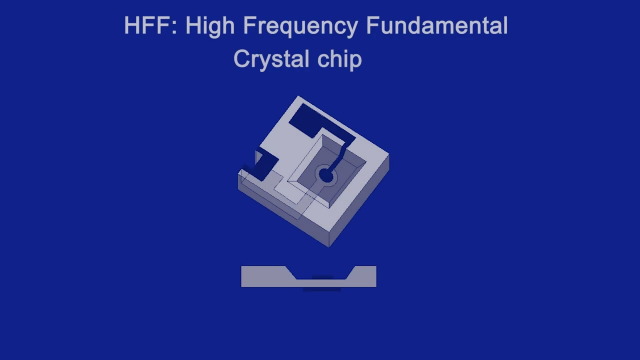
評論