上期介紹了TGV技術(shù)的國內(nèi)外發(fā)展現(xiàn)狀,今天小編繼續(xù)為大家介紹TGV關(guān)鍵技術(shù)新進展。TGV工藝流程中,成孔技術(shù),填充工藝為兩大核心難度較高。
成孔技術(shù)
TGV成孔技術(shù)需兼顧成本、速度及質(zhì)量要求,制約著TGV技術(shù)的發(fā)展。經(jīng)過多年的積累,業(yè)界及學界許多研究工作都致力于研發(fā)低成本、快速可規(guī)模化量產(chǎn)的成孔技術(shù),追求高速、高精度、窄節(jié)距、側(cè)壁光滑、垂直度好的TGV質(zhì)量目標。TGV通孔的制備方法包括噴砂、機械鉆孔、干法刻蝕、濕法腐蝕、聚焦放電等,目前,激光誘導刻蝕法具有高速度、無需掩膜等優(yōu)點,或?qū)⒊蔀槲磥碇髁鳌?/p>
1)磨料噴射加工(AJM)
AJM利用磨料噴流對玻璃基板表面進行處理,玻璃材料因脆性侵蝕產(chǎn)生裂紋和碎片,最終形成特定的孔狀形狀。AJM工藝通常使用Al2O3、石榴石、SiC或金剛石顆粒等磨料,用于加工大尺寸、高厚度的多種基材,如金屬、玻璃、陶瓷、聚合物和復合材料,能夠制備盲孔和通孔,成孔過程中需要在玻璃基板表面上沉積抗磨料顆粒的金屬或聚合物保護未加工區(qū)域。AJM是一種非熱加工方法不影響材料性能,可在無塵環(huán)境中使用,包括磨料漿噴射、磨料水噴射和磨料空氣噴射工藝,廣泛應(yīng)用于半導體制造、電子器件、微流體通道和微機電系統(tǒng)(MEMS)。
AJM在玻璃切割和鉆孔領(lǐng)域的研究相對成熟,沖擊角、噴射壓力、噴嘴距離、噴嘴內(nèi)徑和磨料在噴射中的質(zhì)量百分比是主要的工藝參數(shù),目前Al2O3是主要的磨料,粒徑從5μm到100μm不等,磨料越小TGV內(nèi)粗糙度越小,通常AJM在空氣環(huán)境中成孔速度為0.1μm/s~32μm/s,在漿液環(huán)境中成孔速度為0.6μm/s~4.4μm /s,單面成孔形態(tài)為錐形孔,正反面對稱加工成孔形態(tài)為雙錐形通孔,更適合處理大尺寸、厚玻璃基板中的低視角比的TGV。
2)電化學放電加工(ECDM)
ECDM是一種利用火花放電產(chǎn)生的高溫和沖擊使熔化的玻璃從基板飛濺出去,在玻璃中形成通孔的成孔方法,成本較低,是比較理想的加工玻璃等非導電硬脆性材料的加工方式。玻璃通孔的內(nèi)壁經(jīng)過火焰拋光,直到非常光滑,殘余應(yīng)力通過后處理退火來消除,可對厚度100μm~500μm的石英、鈉鈣硅和無堿玻璃加工成孔,而不需要面罩或無塵環(huán)境,為防止厚玻璃在鉆孔過程中會產(chǎn)生更多的玻璃濺射,最優(yōu)的加工厚度為100μm至200μm。ECDM成孔時間為0.2秒~0.5秒,并可通過多個放電端口同時執(zhí)行,處理的孔徑和形貌與電極尺寸和表面粗糙度有關(guān)。
在熔融石英襯底上制造 3D 電感器的示意圖,(a) 熔融石英襯底,(b) 通過 ECDM 制造的 TGV,(c) 粘合到載體襯底的襯底,(d) 電鍍銅,(e) 拋光掉銅種子層,(f) 兩側(cè)沉積 Ti/Cu 層,(g) 兩側(cè)光刻以確定RDL模具,(h) 電鍍銅、光刻膠去除和種子層濕法蝕刻
圖源:Recent Progress of TGV Technology for High PerformanceSemiconductor Packaging,Joumal of Welding and Joining 作者:Beom Chang Seok, Jae Pil Jung
DOI:https ://doi.org/10.5781/JWJ.2024.42.2.2
3)光敏玻璃成孔技術(shù)
光敏玻璃是通過將光敏劑引入玻璃體中,形成的一種感光玻璃,光敏玻璃成孔是將光敏玻璃在特定波長的光線下發(fā)生化學反應(yīng),再經(jīng)過熱處理后完成指定區(qū)域的改性,經(jīng)化學蝕刻后成型TGV。常用的光敏玻璃,如2016年肖特開發(fā)的FOTURANI玻璃,在紫外線照射下會發(fā)生光化學反應(yīng),將玻璃加熱至500-600°C結(jié)晶化處理,再用氫氟酸蝕刻改性的玻璃基板,其速率比未改性區(qū)域高20-50倍。光敏玻璃可以通過紫外激光照射或無掩膜改性,這兩種加工方法都能夠加工深寬比超過8的TGV,孔道內(nèi)壁具有良好的垂直度(傾角低至1°)和粗糙度(小于1μm)。光敏玻璃成孔技術(shù)中曝光均勻性不佳和曝光時間增加等問題,對光敏玻璃通孔質(zhì)量易造成影響,而玻璃基板的高成本和加工的復雜性等問題也是當前面臨的技術(shù)應(yīng)用挑戰(zhàn)。
4)激光燒蝕(LD)
LD是通過熱沖擊和燒蝕形成低直徑和高深寬比的TGV成孔技術(shù),利用玻璃基板對特定波長的激光的強吸收特性,將激光束聚焦在基板表面,使玻璃氣化或者離子化,如圖1所示。用于TGV工藝的常用激光器包括紅外CO2激光器、紫外UV-YAG激光器和ArF準分子激光器。LD可實現(xiàn)快速加工,適合大規(guī)模生產(chǎn),但在激光加工熱應(yīng)力的作用下TGV內(nèi)部易形成微裂紋等損傷和邊緣易凸起等缺點。可通過在玻璃表面添加有機層以減少激光損傷,將玻璃浸入冷卻液體中減少熱沖擊,加工前對玻璃進行預熱,或使用較短的脈沖激光等工藝改善。
圖1 LD工藝簡圖
5)激光誘導深度蝕刻(LIDE)
激光誘導深蝕刻技術(shù)使用激光改性玻璃基板以形成待刻蝕區(qū)域,將玻璃基板置于氫氟酸或堿性溶液中刻蝕,激光誘導區(qū)域的蝕刻速率遠遠高于其他區(qū)域,從而形成通孔。與氫氟酸相比,堿性的蝕刻率較低,但更易形成具有高長寬比的近垂直通孔。石英玻璃和硼硅酸鹽玻璃的蝕刻率高于其他類型的玻璃,可以加工直徑小于7μm、深寬比高達50、70甚至100的玻璃通孔。通過多個LIDE工藝,可以實現(xiàn)同一玻璃基板上不同直徑的通孔和盲孔的集成,如圖2所示。LIDE工藝加工大尺寸的通孔時間長,效率低,加工前需要對盲孔設(shè)定點間距,這些盲孔連接起來形成空腔。腔體的處理時間取決于激光誘導的點間距和激光的行進速度,點間距越大,空穴底部的粗糙度越高(Ra>0.1μm),而過小的點間距會導致激光感應(yīng)過程中玻璃內(nèi)部的積熱問題,影響加工結(jié)果。
圖2 玻璃基板上不同直徑的通孔和盲孔
LIDE適用于處理任意尺寸和間距的孔道或盲孔陣列。它能夠通過封閉連接間隔緊密的孔(1-10μm)來創(chuàng)建任何形狀的腔或大孔。成孔質(zhì)量均勻,一致性好,無裂紋;成孔速率快,可達到290 TGV/S;TGV形貌可調(diào),由于刻蝕的各向異性,可以通過調(diào)節(jié)激光參數(shù)來控制 TGV的垂直度和形貌。LIDE成孔技術(shù)在速度、質(zhì)量和成本方面具有多方面的優(yōu)點。可處理范圍廣泛的TGV,與其他工藝具有高度兼容性,在三維集成和晶圓級封裝領(lǐng)域具有很高的應(yīng)用潛力。激光誘導刻蝕優(yōu)勢明顯,已被康寧,肖特,AGC,MosaicMicrosystems,LPKF,Plan Optik,Samtec和廈門Sky-semi等企業(yè)廣泛采用,在成孔技術(shù)中脫穎而出。
金屬填充技術(shù)
在TGV技術(shù)中,填充導電材料是確保電氣連接的關(guān)鍵步驟。TGV金屬填充技術(shù)不僅需要確保金屬在TGV內(nèi)的均勻填充,還需要確保金屬層與玻璃基板的緊密結(jié)合,任何不均勻、不緊密的填充都可引起導電性能及可靠性的降低。TGV技術(shù)中高質(zhì)量的金屬填充則是另一難點,TGV主要有盲孔、垂直通孔、X型通孔以及V型通孔四種類型,這些形狀對導電材料的沉積構(gòu)成了較大的挑戰(zhàn),容易形成孔的“堵塞”,玻璃襯底與金屬層之間的分層,金屬層卷曲甚至脫落的現(xiàn)象,通過選擇合適的導電材料和優(yōu)化填充工藝,可以實現(xiàn)高效、可靠的電氣連接。常用的導電性能良好的填充材料包括銅、銀或金等金屬,填充方式通常包括金屬導電膠填充法和電鍍填充法。
1)金屬導電膠填充法
金屬導電膠填充材料可選用納米銀漿和導電銅漿,通電后具有可調(diào)節(jié)的CTE,與玻璃接近。金屬導電膠可以通過絲網(wǎng)印刷和燒結(jié)填充到TGV中實現(xiàn)電互聯(lián)或者使用3D打印工藝,使用小型噴嘴噴出金屬導電膠,配合使用激光燒結(jié)膠體,形成電互聯(lián),在真空環(huán)境下,可以避免糊狀物內(nèi)部的空隙。金屬導電膠填充法可以實現(xiàn)高縱橫比和高密度的TGV陣列金屬化。固化后,金屬導電膠的體積可能會收縮,導致TGV中的凹陷缺陷,通過重新填充糊狀物或研磨玻璃基板來去除該凹陷。印刷和填充過程后,玻璃基板表面仍有殘留物,燒結(jié)后,需要對玻璃的表面進行拋光等處理,以提高其表面清潔度。 金屬導電膠填充法在TGV金屬化的應(yīng)用研究較少。Iwai等人利用銅錫導電填料填充TGV,經(jīng)真空熱壓完成燒結(jié),實現(xiàn)多層玻璃基板內(nèi)通孔的垂直互連。Takahashi等人通過3D打印和絲網(wǎng)印刷在直徑為50μm、間距130μm的TGV內(nèi)實現(xiàn)了導電銅膏的填充,其中銅膏的表面電阻率約為1.6-1.9 Ωm/sq。 廈門大學陳力等人使用導電銀棒在400微米厚的BF33玻璃基板上成功填充了50微米和100微米直徑的TGV。填充的通孔沒有氣泡等缺陷,并且過孔內(nèi)的銀膏的電阻率為2.56×10-7Ω·m。唐平高等人利用噴墨打印填充盲孔,對填充金屬液后的盲孔進行真空干燥處理,形成所述金屬填充層,再減薄玻璃襯底厚度,形成能夠貫穿玻璃襯底的通孔,減少整體制備時間,提高生產(chǎn)效率。 通常,金屬導電膠的導電性低,并且在燒結(jié)過程中其電阻率變化。金屬導電膠填充法適用于應(yīng)用具有低電互連標準或高縱橫比的TGV金屬化,但工藝穩(wěn)定性仍有待提高。
2)磁控自組裝方法
針對不同的縱橫比和傾斜角度的TGV金屬化,Laakso等人采用磁場輔助的自組裝方法,將鎳線固定在TGV內(nèi),實現(xiàn)電氣互連。切割的鎳線在磁場作用下進入到玻璃通孔中,采用SOG技術(shù)填充孔洞,并用甲基硅氧烷固化,固化后,在正面布線完成后,使用背面濕法蝕刻來薄化晶片并去除鎳線,從而完成TGV金屬化。這種方法能夠?qū)崿F(xiàn)具有高密度、高縱橫比和低電阻值的TGV金屬化,同時可確保金屬棒與各種內(nèi)壁形態(tài)和粗糙通孔的兼容性,調(diào)整金屬棒和SOG的成分可以緩解TGV中的感熱失諧問題。該工藝對磁場控制技術(shù)有嚴格的要求,磁控制導線的長度必須大于寬度才能實現(xiàn)正確的定向,由于蝕刻劑需穿透SOG和TGV的側(cè)壁,給HF蝕刻薄化晶片增加了難度,通常采用化學機械研磨方法實現(xiàn)晶片減薄。
3)電鍍法
電鍍法填充是一種在TGV內(nèi)壁進行金屬化處理的技術(shù),主要包括:
金屬化前處理,通過物理氣相沉積(PVD)、化學氣相沉積CVD等技術(shù)在孔壁上形成一層薄的導電層(如種子層),對玻璃通孔進行預處理,以提高金屬化的附著力和均勻性,種子層材料可以是Ti/Cu、Cr/Cu等;
電鍍填孔,將玻璃通孔放入電鍍槽中,并注入適當?shù)碾娊庖海ㄟ^電流的作用,在孔壁上沉積形成金屬層,電解液的選擇對電鍍層的質(zhì)量和性能有重要影響,電鍍時間以及電流的密度是影響金屬層厚度和均勻性;
電鍍后處理,通過濕腐蝕和CMP等方法去除殘留的電解液和雜質(zhì),對金屬層進行后處理,如拋光、清洗等,去除雜質(zhì)、提高表面光潔度和耐腐蝕性。
當前,TGV電鑄銅實心填充主要有3種方法,一種是借助新型鍍銅添加劑并配合電流密度調(diào)整,實現(xiàn)通孔1/2處在電鑄過程中加速生長并發(fā)生橋接,從而將TGV填充轉(zhuǎn)換為2個盲孔填充。第二種是先雙面保形電鑄加厚側(cè)壁銅層,隨后更換鍍液填實一端孔口,這種填充方式也稱為“蝶形填充 (butterfly mode1)”。第三種也是最為常見的方法,通過將雙面TGV固定在陰極上或預先填充某側(cè)孔口使之轉(zhuǎn)變成盲孔,再以“自下而上(bottom-up)”方式進行實心填充。由于繼承了TSV鍍銅工藝技術(shù)的基礎(chǔ),自下而上的鍍銅實心填充在電學特性、熱力學可靠性、工藝開發(fā)難度等方面更具優(yōu)勢。 TGV孔徑相對比較大且多為通孔,增加了電鍍法填充電鍍時間和成本,并且由于玻璃表面平滑,與銅的黏結(jié)力較差,玻璃基板與金屬層之間的出現(xiàn)分層現(xiàn)象,甚至出現(xiàn)金屬層的脫落,同時電鑄銅添加劑作用機理復雜,且添加劑成本高昂。 為解決以上問題,研究者從種子層、電解液等方面開展了大量工作。CN113066758B提供了一種TGV深孔填充方法,對玻璃基板以及玻璃通孔進行腐蝕后再填充,可在一定的程度上防止種子層脫落,保證填充效果;CN116913861A公開了一種TSV/TGV微通孔金屬化方法,通過設(shè)置多段電流密度和時間,調(diào)整通孔兩端的電力線密度,精準控制橋連位置,完成多種方法的部分實心填充。Tanaka等人針對深度為300μm、底部直徑為60μm、頂部直徑為40μm的TGV完成了部分電鍍填充,并通過對電流分布的模擬分析研究了電鍍法填充的可行性。在此基礎(chǔ)上制備的共面波導(CPW)中,TGV在30GHz下的插入損耗為0.2dB。王等人采用雙面銅共同電鍍工藝實現(xiàn)了X形TGV的填充,在-40°C至125°C的100次熱循環(huán)實驗中,在關(guān)鍵部位未觀察到裂紋等缺陷。這表明電鍍填充TGV工藝在制備MEMS器件方面具有良好的應(yīng)用前景。廈門大學陳力等人實現(xiàn)了縱橫比為7的玻璃盲孔電鍍和縱橫比為4的雙面TGV電鍍。
面臨的技術(shù)問題與挑戰(zhàn)
近年來,由于玻璃材料的易碎性和化學惰性,當前已有的TGV技術(shù)都還存在許多問題,距離實際應(yīng)用和大規(guī)模的量產(chǎn),還有很長的路要走。截至目前,TGV通孔技術(shù)發(fā)展在制造和應(yīng)用過程中面臨著一系列技術(shù)問題和挑戰(zhàn)。主要包括: 1)成孔技術(shù)難度大,目前缺乏類似TSV的深刻蝕工藝,難以快速制作高深寬比的TGV。現(xiàn)有的方法仍存在損傷玻璃,造成表面不光滑,生產(chǎn)良率低、加工效率低,無法實現(xiàn)大規(guī)模量產(chǎn)等問題難以解決; 2)TGV的高質(zhì)量填充技術(shù),與TSV不同,TGV孔徑相對比較大且多為通孔,電鍍時間和成本將增加。目前填孔工藝的難點,一方面是孔徑與孔深的精準控制,填孔工藝中需確保填孔尺寸和深度的準確性,從而保證金屬填充能夠完全覆蓋通孔,并且實現(xiàn)均勻的填充量,這就需要通過精確的工藝參數(shù)設(shè)定和先進的設(shè)備技術(shù)來實現(xiàn)。另一方面是填孔材料選擇,在TGV技術(shù)中,填孔材料它不僅要與玻璃基板具備良好的相容性,還需提供出色的粘附性和導電性。在材料的選擇上,需綜合考慮其熱膨脹系數(shù)、化學性質(zhì)以及成本效益等多方面因素,確保所選填孔材料能夠滿足TGV技術(shù)的嚴格要求。 3)缺乏可靠性數(shù)據(jù),當前各個廠家TGV技術(shù)的制備方法不盡相同,產(chǎn)品良率和成本的控制是大家共同面臨的挑戰(zhàn)。亟需建立一個可行的商業(yè)生產(chǎn)生態(tài)系統(tǒng),統(tǒng)一標準化生產(chǎn)、組裝和測試工藝方法和設(shè)備,形成穩(wěn)定的制備工序,建立TGV技術(shù)可靠性數(shù)據(jù)庫。 4)層數(shù)限制:隨著技術(shù)的不斷發(fā)展,對TGV的要求越來越高,特別是在多層結(jié)構(gòu)的應(yīng)用中。然而,由于玻璃基板的材料特性和TGV技術(shù)的限制,其層數(shù)受到一定的限制。層數(shù)過多會導致結(jié)構(gòu)復雜、加工難度大、成本增加等問題。因此,如何在保證性能的前提下提高層數(shù)成為了當前面臨的一個重要問題。 為了解決這些問題和挑戰(zhàn),需要不斷加強國內(nèi)TGV技術(shù)的研發(fā)和工藝優(yōu)化,提高TGV產(chǎn)品質(zhì)量和性能;同時,也需要關(guān)注市場需求和國內(nèi)外TGV技術(shù)趨勢的變化,不斷調(diào)整產(chǎn)品結(jié)構(gòu)和生產(chǎn)策略。
-
磁控
+關(guān)注
關(guān)注
0文章
13瀏覽量
11371 -
電鍍
+關(guān)注
關(guān)注
16文章
459瀏覽量
24156
原文標題:TGV技術(shù)中成孔和填孔工藝新進展
文章出處:【微信號:深圳市賽姆烯金科技有限公司,微信公眾號:深圳市賽姆烯金科技有限公司】歡迎添加關(guān)注!文章轉(zhuǎn)載請注明出處。
發(fā)布評論請先 登錄
相關(guān)推薦
玻璃通孔(TGV)技術(shù)原理、應(yīng)用優(yōu)勢及對芯片封裝未來走向的影響
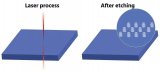
一文了解玻璃通孔(TGV)技術(shù)
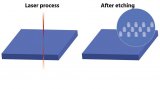
玻璃通孔(TGV)技術(shù)在傳感器制造和封裝中的應(yīng)用
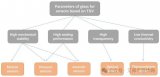
HDI盲埋孔工藝及制程能力你了解多少?
高性能半導體封裝TGV技術(shù)的最新進展
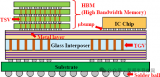
先進封裝中互連工藝凸塊、RDL、TSV、混合鍵合的新進展
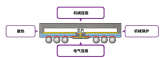
芯片和封裝級互連技術(shù)的最新進展
5G新通話技術(shù)取得新進展
PCB盲孔、埋孔和通孔是什么
HDI線路板盤中孔處理工藝
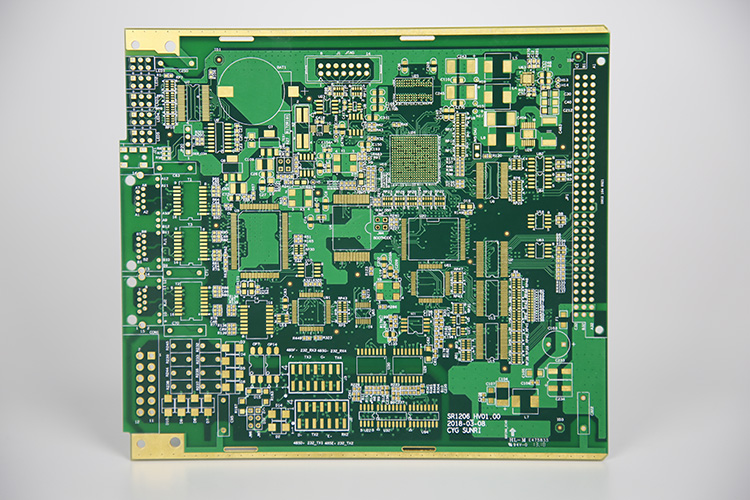
評論