在傳統汽車零部件生產模式中,機床上下料依賴人工操作,不僅消耗大量人力與時間,效率低下,還難以保證產品品質的均一性。明達技術洞察行業痛點,為汽車零部件行業量身打造了一套先進的機床自動上下料解決方案,助力企業實現生產效率、產品質量與管理水平的全方位飛躍。
業務困境
人工上下料的多重弊端:人工承擔上下料任務,不僅工序繁瑣耗時,而且受限于人力極限,整體生產效率難以提升。同時,人工操作過程中存在安全風險,一旦操作失誤,極易引發人身傷害事故。另外,上下料的精準度與穩定性高度依賴操作人員的個人技能和經驗,這不可避免地導致產品加工質量波動,難以滿足大規模、標準化的生產需求。
數據記錄與管理難題:生產數據的記錄工作全靠人工手動完成,例如每日產量等關鍵數據,不僅耗費人力,而且數據整理過程復雜,容易出現記錄錯誤、數據丟失或難以快速檢索的情況,嚴重影響企業對生產過程的有效把控與分析決策。
設備狀態監控滯后:機床設備的管理主要依賴人工巡檢,維護人員無法實時掌握設備的運行狀態。當設備突發故障時,往往是現場操作人員發現后才反饋給維護人員,由于設備數據信息不透明,故障排查工作耗時費力,經常導致生產進度延誤,給企業帶來不必要的經濟損失。
明達新方案
面對這些挑戰,明達技術的工程師團隊深入企業,開展了全面的項目前期調研,并與客戶進行了充分的技術方案交流。在此基礎上,團隊負責從設計、仿真、機械設備制造,到現場設備安裝、調試、投產的全流程數字化升級改造工作。
明達技術提供的機床上下料機構,由多個核心部分構成,包括上料機構、桁架機械手機構、過渡線模組機構、下料線機構以及抽檢臺機構等。
系統運行時,人工先將工件放置在上料機構,隨后桁架機械手迅速抓取工件,精準放置到機床內進行加工。加工完后,桁架機械手將工件從機床取出,移送至過渡線。過渡線抓手接過工件,傳遞到下一個桁架機械手的取料位置,以便進行下一輪加工。最后,當工件完成所有加工工序,由最后的桁架機械手將其放置到下料線,下料線抓手抓取工件后,送往去毛刺機構進行處理。
此外,該項目還實現了設備數據的實時采集。通過 PLC 以及MBox20網關系統,能夠實時讀取設備的運行狀態、產量等關鍵數據,并以大屏數據看板的形式呈現,讓車間管理人員對設備狀態一目了然,實現了設備管理的透明化與智能化。
顯著收益
通過明達技術定制化的數字化產線升級改造,該汽車零部件企業成功邁入了自動化生產的新階段。機床自動上下料機構的投入使用,使工件上下料效率提高了 20% 以上,徹底消除了傳統人工操作帶來的安全隱患。同時,設備數據的實時采集與可視化展示,實現了設備運行狀態的實時反饋,設備綜合效率(OEE)提升了 15% 以上,有力推動了企業生產效益與競爭力的提升。
審核編輯 黃宇
-
智能化
+關注
關注
15文章
4916瀏覽量
55550 -
機床
+關注
關注
1文章
587瀏覽量
30304 -
數字化
+關注
關注
8文章
8806瀏覽量
61969
發布評論請先 登錄
相關推薦
明達助力構建智能變電站新體系
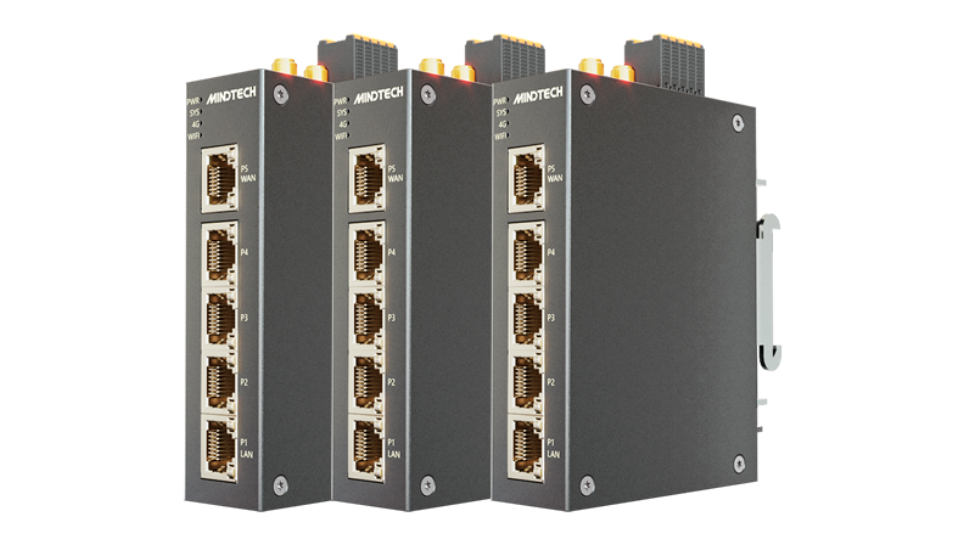
新技術解決方案 復合機器人 CNC 自動上下料
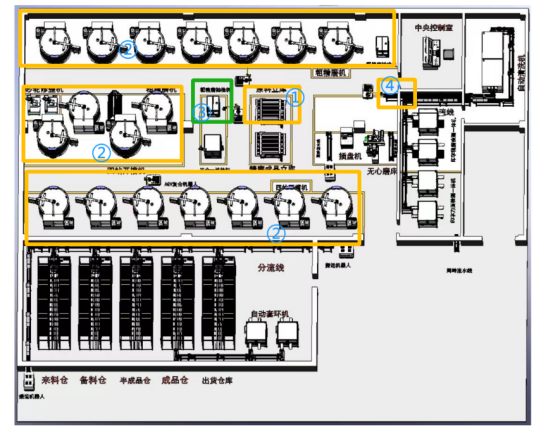
明達IO——助力冶金設備智能化升級
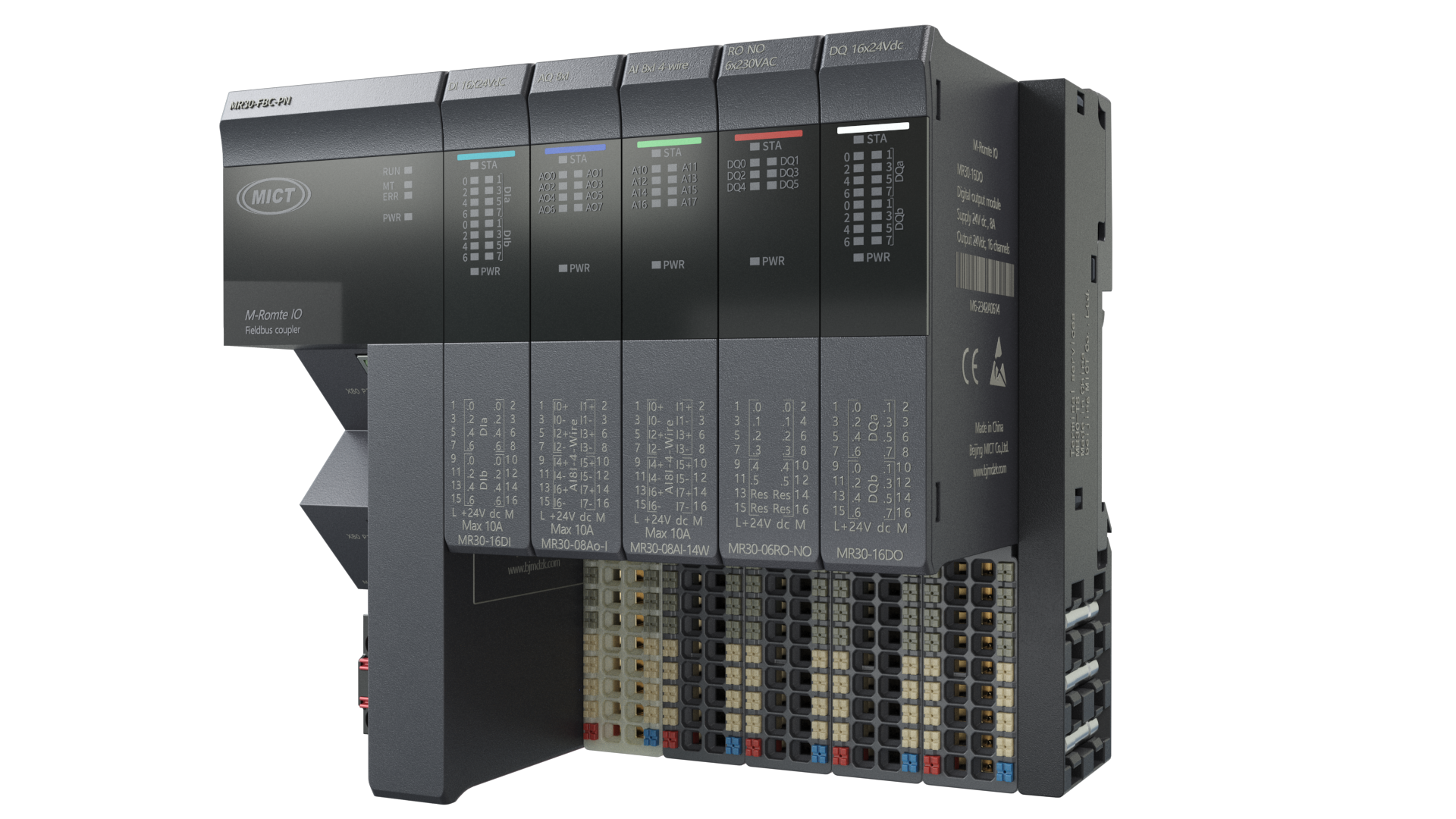
明達IO引領輕工紡織智能化轉型
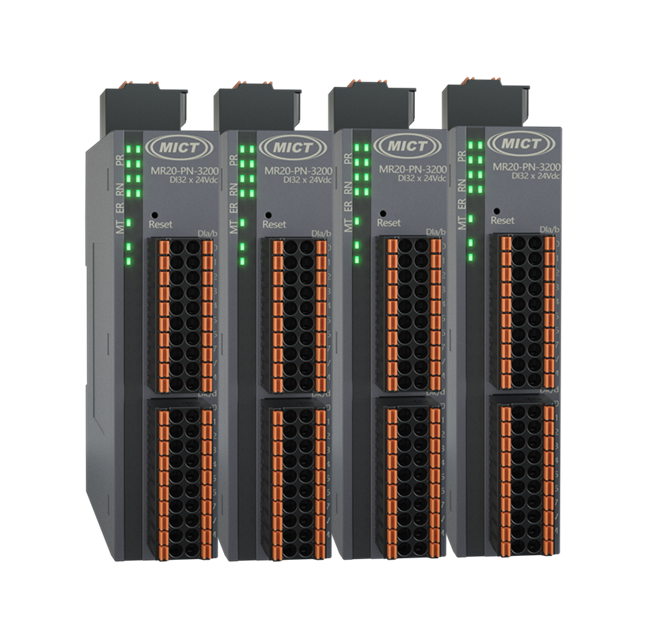
CNC機床加工上下料自動化解決方案
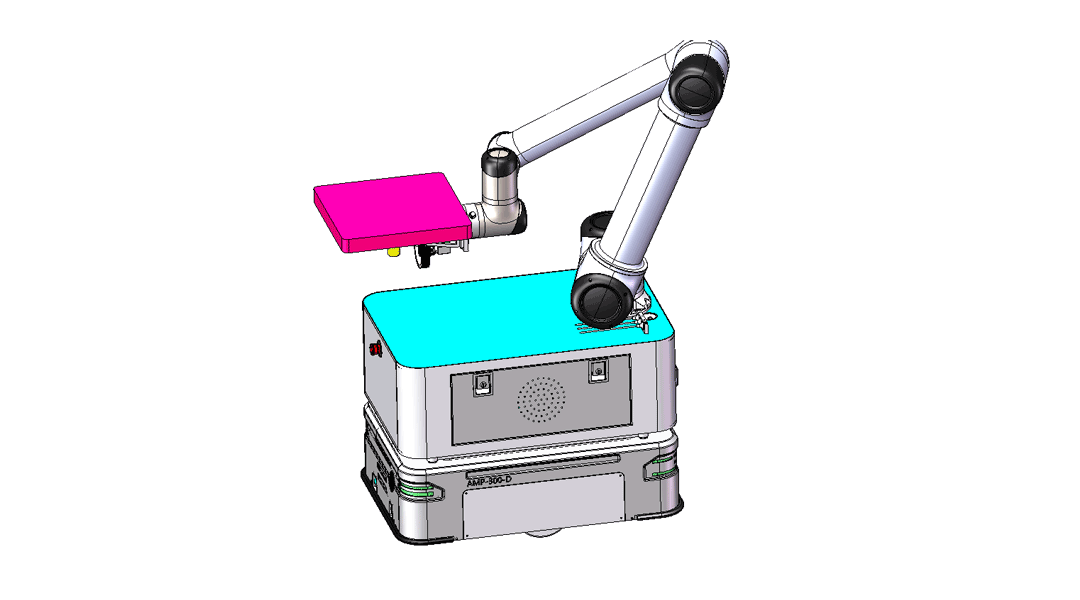
富唯智能鍍膜上下料設備通過智能化控制系統實現了對生產流程的精準監控和調整
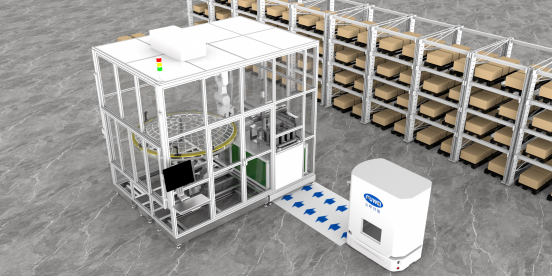
訊維智能可視化綜合平臺:打造高效遠程會議的新體驗
會議一體機:打造智能化、高效化的會議新體驗
富唯智能案例|3D視覺引導機器人抓取鞋墊上下料
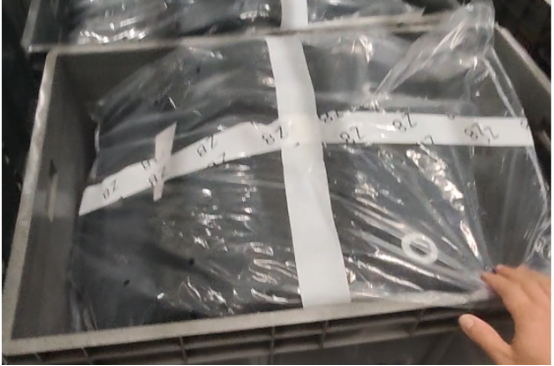
機器人上下料為汽車制造車間實現高效自動化
高效、安全、智能:機器人如何重塑行業內部物流上下料流程?
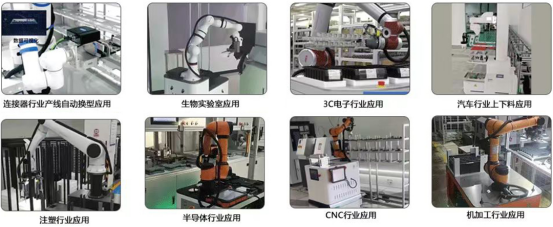
cnc加工中心,機床上下料正面臨著自動化轉型
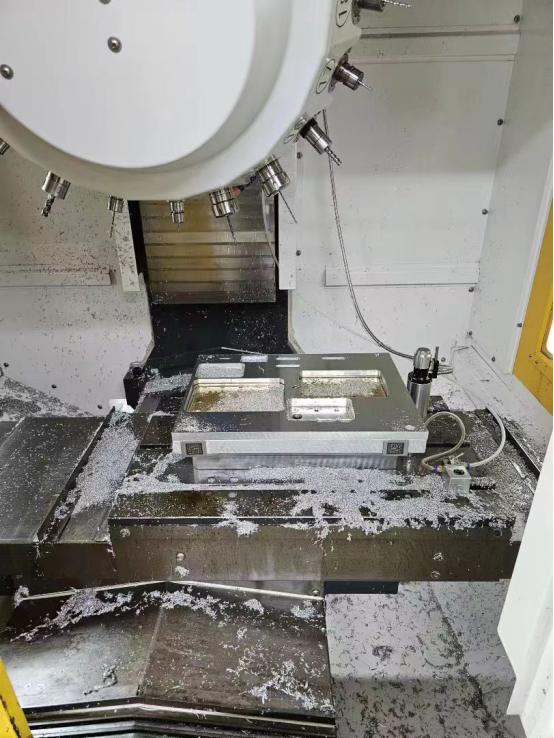
評論