為什么汽車電子Pin針檢測需要近乎完美的良率?
在新能源汽車、智能駕駛快速發展的今天,車載芯片的Pin針間距已縮小至0.2mm級,而檢測精度必須達到±3μm,否則可能導致電池故障、系統失靈等致命風險。華頡科技作為國產智能檢測領域的領軍企業,通過自主研發的高精度AOI光學方案,助力某新能源車企將Pin針檢測良率從99.5%提升至99.99%。本文拆解這一工業4.0標桿案例,揭秘華頡AOI如何實現微米級檢測與行業痛點的“精準破局”。
一、核心技術:華頡AOI如何突破汽車電子檢測極限?
1. 微間距檢測的“光學難題”與華頡解決方案
● 挑戰:0.18mm間距Pin針因金屬反射、陰影遮擋導致傳統CCD成像模糊,漏檢率高達0.5%。
●方案:
硬件創新:搭載2000萬像素線陣CCD與多光譜光源(白光+紅外光+紫外光),消除干擾。
算法升級:基于深度學習的缺陷分類模型,誤檢率<0.1%,支持焊盤污染、高度差、歪斜三類缺陷實時識別。
●實測數據:
檢測精度:±3μm,達國際先進水平。
速度:單線產能2000UPH,效率提升100%。
2. 功能安全認證的“技術壁壘”
●需求:ISO 26262要求缺陷逃逸率<0.01%,但傳統設備無法滿足。
●華頡突破:
雙冗余光學系統:確保檢測結果一致性。
全生命周期追溯:每顆芯片生成檢測報告二維碼,支持數據溯源。
二、工業4.0實戰案例:華頡助力某車企BMS芯片檢測升級
案例背景
●產品:新能源汽車BMS(電池管理系統)芯片,Pin針間距0.18mm,需滿足ISO 26262功能安全認證。
●痛點:
傳統設備漏檢率0.5%,導致年均200萬元返工成本。
客戶投訴率上升,面臨車企供應商資格風險。
解決方案
●硬件配置:
高精度AOI設備:100倍微距鏡頭+激光共聚焦光源,消除陰影干擾。
工業4.0模塊:集成MES系統,實現檢測數據實時上傳與產線自動預警。
●算法優化:
動態閾值調整:根據Pin針類型自適應優化檢測參數。
缺陷分類模型:支持**焊盤污染(>2μm2)、高度差(>1μm)、歪斜(>0.3°)**精準識別。
成果
●良率提升:從99.5%躍升至99.99%,年減少缺陷芯片12,000顆。
●成本節省:
返工成本:降低80%(年均200萬元→40萬元)。
認證通過:通過ISO 26262認證,成為車企全球供應商。
三、挑戰應對:華頡AOI的“技術硬核”
1. 極端環境下的穩定性保障
●技術亮點:
溫控系統:設備內部溫度恒定在23±0.5℃,消除熱漂移影響。
六軸減震平臺:振動影響降低90%,適應產線復雜環境。
2. 高速檢測與精度平衡
●創新點:
多相機并行架構:實現2000UPH產能,效率翻倍。
邊緣計算:本地化AI推理,延遲<50ms,支持實時決策。
3. 量子點光源技術:下一代檢測方案預演
●技術儲備:
單色性>95%的量子點光源,可識別0.05μm級缺陷(已應用于華頡實驗室原型機)。
四、選型指南:如何選擇高良率Pin針檢測方案?
1. 核心指標與華頡方案解析
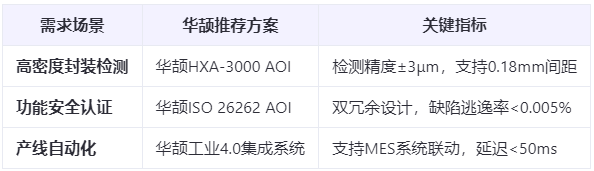
2. 選型三步法
明確精度需求:是否需檢測0.18mm以下間距?
匹配產線速度:是否需支持**>1500UPH**?
-
汽車電子
+關注
關注
3031文章
8137瀏覽量
168625 -
PIN
+關注
關注
1文章
311瀏覽量
24823
發布評論請先 登錄
相關推薦
光頡高精度車規電阻選型:薄膜VS厚膜,0.01%精度如何滿足汽車電子嚴苛需求?
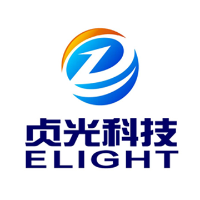
三星電子1c nm內存開發良率里程碑推遲
三星1c nm DRAM開發良率里程碑延期
傳三星電子12nm級DRAM內存良率不足五成
為什么說“AOI檢測”是SMT焊接質量的把關者?
M12航空插頭4pin插針折彎工藝
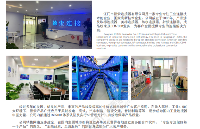
評論