引言
由于壓電陶瓷執行器(Piezoelectric Actuator,PZT)具有定位精度高、帶寬大、響應時間快等優點,所以被廣泛地應用于如超精密加工、半導體光刻等領域的精密定位系統中。但是隨著工業化生產對產率要求的不斷提高,在滿足定位精度要求的同時,對定位速度提出了越來越嚴格的要求。如何實現快速而精確的定位控制,如何準確評價控制算法的性能顯得尤為重要。
對于PZT定位精度控制的研究主要集中于逆模型的建立,無論是基于現象的Preisach模型,還是具有明確函數表達式的Duhem模型,都可以有效補償遲滯與蠕變效應帶來影響,獲得高精度的定位控制。對于定位速度控制的研究,無論是動態性能更好的壓電器件的使用,還是點到點運動控制算法的優化與應用,都取得了高速度的定位控制?;诂F有的PZT,三階軌跡規劃方法可以獲得高精度、高速度的控制效果。
由于三階軌跡規劃算法離散化迭代計算的時間因子為控制系統的單位伺服周期,而以往的非實時計算平臺,無法提供分辨率足夠小的伺服周期,也就無法保證在算法開發驗證階段對其性能進行評價的準確性。
xPC Target采用主機與目標機結合的方式,目標機運行的實時內核可以在足夠短的時間內計算控制算法的仿真模型,為三階軌跡規劃算法的實時執行及性能評價提供了有效的途徑。本文建立基于xPC Target 的PZT微動控制半實物仿真平臺,對PZT的微動控制算法進行研究與驗證,以獲得高精度、高速度的PZT微動控制。
1 系統硬件設計
PZT 微動控制半實物仿真系統硬件結構如圖1 所示,整個系統硬件結構由以下幾個部分組成:處于用戶層的宿主機、處于中間層的xPC Target目標機和處于執行器層的PZT 驅動/控制系統。其中,宿主機采用PC機,運行Matlab/Simulink/RTW 環境,控制算法的Simu-link模型在此環境上開發設計、編譯及下載到目標機中執行;仿真過程中由目標機運行xPC Target實時內核以及控制算法,目標機采用ADVANTECH 公司的PWS-1409TP便攜式工控機,通過以太網與宿主機連接;目標機主板上加裝NI公司的PCI-6229多功能數據采集卡,通過此數據采集卡的模擬信號通道與執行器層的PZT控制系統連接;PCI-6229配備32通道16位模擬輸入端口,最高采樣率為250 kHz;4通道16位模擬輸出端口,最高采樣率為933 kHz,可以確保整個半實物仿真系統實現亞毫秒的伺服周期。PZT 控制系統由PhysikInstrumente 公司的E-712 驅動/控制箱、N-111 型PZT 以及D-E30型電容傳感器組成。
2 控制算法設計
2.1 控制算法分析
對于典型的閉環運動控制方法,經過離散化之后,在每個伺服周期內,位移的測量值都與同一個給定值進行比較[10].因此,在運動初始的若干個伺服周期內,測量值與給定值偏差會很大,而在臨近運動結束的若干個伺服周期內測量值與給定值的偏差又會很小,如果PID控制器參數保持不變,無疑會在啟動或者結束階段產生相對較大的殘余振動,既降低了控制精度,又增加了調節時間。
三階軌跡規劃方法以執行器可達到的最大速度、最大加速度以及最大沖擊為輸入參數,計算獲得的運動軌跡更為平滑,離散化后,將離散值作為不同伺服周期內不同的給定值,就可以減小上述的殘余振動,改善動態響應。典型的三階對稱軌跡規劃輪廓如圖2所示。
通過對圖2(a)與圖2(b)相應軌跡曲線的比較可知:輸入條件不同時,相應的軌跡形狀并不相同。如何實現設計有效的算法計算出不同形狀的軌跡,是三階軌跡規劃方法面臨的主要問題。
通過對圖2(a)與圖2(b)的進一步分析可知,雖然軌跡輪廓有所不同,只要是對稱的三階軌跡,都可以由3 個時間惟一確定:即最大速度持續時間tv ,最大加速度持續時間ta ,最大沖擊持續時間tj .這3個時間數值的不同決定了三階軌跡的不同形狀。
2.2 控制算法實現
以上文的3個時間參數為切入點,三階對稱軌跡規劃算法的實現步驟可以分為三個:
第一步,由目標位移、最大沖擊、最大加速度以及最大速度,計算tj 、ta 和tv ,如圖2所示;第二步,由tj 、ta 和tv 計算沖擊跳變的8個時刻:t0 ~t7 ,如圖2所示;第三步,由t0 ~ t7 這8個時間參數作為分段積分的邊界,使用公式(1)所示的多重積分公式,計算每個伺服周期內的位移值,即能得到離散化的三階對稱軌跡。
式中,ts 為伺服周期;Jm 為最大沖擊值;an,vn,sn 分別為tn 時刻加速度值、速度值、位移值。
根據以上分析,使用C語言描述的三階對稱軌跡規劃算法流程圖如圖3所示。
3 系統Simulink 仿真建模
3.1 系統總體模型
在半實物仿真系統的硬件結構的基礎上,借助Matlab/Simulink/RTW環境可以實現控制算法的驗證與評價。
PZT 微動控制系統的Simulink 仿真總體模型如圖4 所示,實現模型主要功能的模塊有三個:軌跡規劃模塊SCurve、閉環PID控制算法模塊、PCI-6229采集卡的A/D和D/A驅動模塊。其中,PCI-6229采集卡的驅動模塊可以在Simulink Library→xPC Target→National Instruments庫中獲得;PID控制算法模塊的參數根據在線仿真進行整定;SCurve 模塊就是三階軌跡規劃算法的Simulink模型。
3.2 三階軌跡規劃模型
前文已完成了C語言描述的三階軌跡規劃的算法,使用Matlab/Simulink 的S-Function Builder 可以方便地將C 語言描述的控制算法轉換為Simulink 環境下的仿真模型。
在Matlab/Simulink 中選擇User-Defined Functions,由其中的S-Function Builder 建立一個函數型Simulink模塊,完成以下兩個步驟,即可獲得如圖5所示的SCur-ve函數型Simulink模塊:
第一步,在Data Properties標簽中,將給定位移sm、最大速度vm、最大加速度am、最大沖擊jm 以及伺服周期Ts定義為輸入端口;將離散化位移軌跡sd、速度軌跡vd、加速度軌跡ad以及沖擊軌跡jd定義為輸出端口;第二步,將三階軌跡規劃算法的C語言文件添加至Libraries標簽下,并將函數聲明添加至External functiondeclaration段落。
3.3 控制算法仿真
為了對三階軌跡規劃算法進行仿真驗證,在圖5所示的Simulink模塊以外引入5個常量模塊及4個示波器模塊:disp為目標位移、vel為最大速度、acc為最大加速度、jerk為最大沖擊、Ts為伺服周期;sd_scope、vd_scope、ad_scope以及jd_scope分別顯示位移、速度、加速度及沖擊的軌跡。
將仿真參數設置為:最大沖擊Jmax = 1 × 108 μm/s3,最大加速度Amax = 1 × 105 μm/s2,最大速度Vmax = 450 μm/s,位移分別為20 μm 和200 μm 時,三階軌跡規劃仿真結果如圖6所示。
由圖6 可見,仿真獲得的軌跡與理論分析相符,S-Function Builder 成功地將C 語言描述的三階軌跡規劃算法轉換成了Simulink模型。
4 實驗與結果分析
完成了如圖1所示的半實物仿真系統硬件搭建,以及如圖4 所示的控制算法仿真驗證后,將Matlab/Simu-link/RTW 環境編譯后的控制算法下載至xPC Target 的目標機中運行,通過實時采樣獲取的數據,對控制算法的性能進行實驗驗證。
將N-111 型PZT 設置為Nanostepping 工作模式,最大沖擊取值1 × 108 μm/s3,最大加速度取值1 × 105 μm/s2,最大速度取值450 μm/s;將PCI-6229 的采樣速率設為1 kHz,即伺服周期為1 ms.位移為200 μm時三階軌跡規劃算法的位移響應曲線與誤差曲線如圖7所示。
由圖7(a)可見,實際位移軌跡精確地跟蹤了理論計算的位移軌跡,半實物仿真平臺的實時性保障了控制算法的性能,沒有出現軌跡滯后現象。由圖7(b)可見,三階軌跡規劃算法可以在0.5 s內實現精度為±1 μm,行程為200 μm的微動控制。
5 結語
本文利用xPC Target技術,建立了壓電陶瓷執行器微動控制半實物仿真系統,研究了壓電陶瓷執行器三階軌跡規劃算法。實驗表明,三階軌跡規劃算法可以實現壓電陶瓷執行器高精度與高速度的微動控制;xPC Target半實物仿真系統可以有效評價控制算法的性能,在對精度與速度要求嚴格的精密定位控制領域中具有一定的應用價值。
-
傳感器
+關注
關注
2552文章
51288瀏覽量
755148 -
控制系統
+關注
關注
41文章
6642瀏覽量
110721 -
以太網
+關注
關注
40文章
5449瀏覽量
172174 -
仿真系統
+關注
關注
1文章
97瀏覽量
20684
發布評論請先 登錄
相關推薦
MathWorks推出xPC Target Turnkey實
基于xPC和CVI的實時仿真系統設計實現
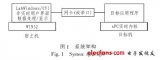
基于RT-LAB的空間對接半實物仿真系統
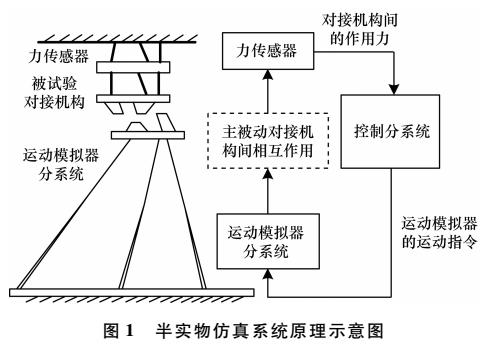
如何使用xPC Target進行TIG焊PID控制實時仿真的資料說明
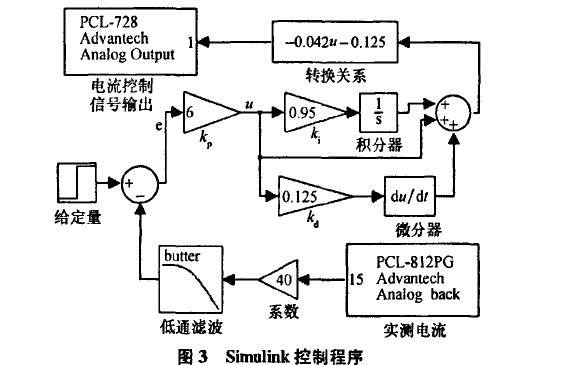
基于dSPACE的飛行器控制半實物仿真系統快速搭建
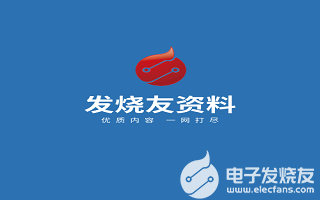
評論