對于當今的汽車制造商而言,產品設計是一個反復迭代的過程,需要計算機輔助工程(CAE)分析師、設計工程師、制造團隊和供應商的共同協作才能成。汽車行業的市場競爭已呈白熱化趨勢,各類新車型的推出令人目不暇接。汽車制造商需要盡可能地提高協作效率、縮短新產品的設計進程,才能在激烈的競爭中贏得優勢。以馬恒達為代表的多家汽車公司,在努力提升產品質量、安全性和可靠性的同時,將著力點放在了革新設計流程上。在仿真 App 的幫助下,馬恒達研發團隊使產品的設計過程變得更具包容性和靈活性,推動企業邁向成功。
產品設計中的難題
不同團隊之間的協作往往是一個非常耗時的過程,這是因為每個團隊都需要以合理、高效的方式整合各自的專業知識。設計工程師在評估新的設計概念或調整現有設計方案時,其中涉及的復雜物理現象會增加工作的難度。擁有專業知識的仿真工程師能夠應對這些極其復雜的問題,他們可以通過詳細的 CAE 分析來幫助設計工程師完成對設計概念的評估。然而多數企業中的仿真工程師人員有限,在面對大量的技術支持需求時常常無法及時交付評估結果。
特定汽車零部件的設計交付時間取決于所需的迭代次數。設計迭代是確保車輛安全性和可靠性必不可少的重要環節。根據設計方案的復雜度,仿真分析可能需要數周到數月的時間才能得到可靠結果。此后,設計團隊根據仿真結果執行設計修改,然后需要再次等待 CAE 團隊進行設計的可行性驗證。
為了贏得這場與時間的競賽,馬恒達研發團隊借助 COMSOL Multiphysics? 多物理場仿真軟件中的“ App 開發器 ”工具,開發了多個用于考察各類穩定桿和底盤設計方案的仿真 App。與傳統方法相比,仿真 App 的使用大幅減少了一款設計在設計團隊和仿真團隊間的迭代次數。
創新的穩定桿設計方法
穩定桿(圖 1)是汽車懸掛系統中的關鍵組件,可防止車輛發生過大的橫向側傾,它通常被設計成一根包含多個彎曲部分的空心或實心梁。設計團隊必須確保穩定桿具有適當的剛度和應力水平,因此他們需要選擇與 CAE 分析師合作,或是向供應商索取驗證報告。CAE 分析師會針對不同的設計創建模型,以準確模擬穩定桿的形變和應力。一旦模型的驗證結果與實驗數據良好吻合,他們就會創建仿真 App。
圖 1. 常見的穩定桿(又稱防傾桿)設計。
穩定桿的仿真 App 支持組建各式各樣的設計配置,僅彎曲部分的樣式就多達 15 種。不僅如此,仿真 App 還提供了空心桿和實心桿選項,如圖 2 所示。最終用戶 (通常是設計團隊的成員)在仿真 App 中輸入彎曲處的坐標來表征穩定桿的幾何形狀,并提供軸承位置、襯套剛度和交叉測試等信息。CAE 分析師通過在仿真 App 中預定義約束條件,方便設計人員簡單快捷地運行準確的仿真,計算穩定桿剛度,并建立標準載荷工況的應力模型,如圖 3 所示。仿真 App 的一般運行時間只有幾分鐘,因此設計團隊可連續運行迭代,實時獲取設計反饋。在了解仿真 App 是基于經過驗證的多物理場模型開發之后,設計團隊對汽車封裝水平信心大增。馬恒達的團隊發現,仿真 App 不僅節省了大量時間,更是促進了企業內部協作。新型的團隊協作文化也有利于員工對最終產品產生更強烈的主人翁意識,由于他們能在一兩天內生成設計方案,減少了對供應商的依賴。
圖 2. 仿真 App 可用于創建幾何圖形以及計算穩定桿的剛度和位移。
圖 3. 使用 App 計算特殊穩定桿配置的剛度得到的仿真結果。
減少底盤的設計迭代
底盤是一個重要的承載部件,它的作用是為車輛提供結構強度,并充當發動機和變速箱等其他零部件的安裝基座。最常見的一種底盤結構是由兩條縱向主梁和多個橫梁組成的梯形車架(圖 4)。橫梁的數量、尺寸、位置和形狀是早期設計階段中需要確定的重要參數。
圖 4. 基于 CATIA? 軟件創建的常見多功能底盤幾何結構。
底盤承受的載荷會產生彎曲和扭轉載荷,這類問題沒有簡單的解析解。解決這類問題的常規方法是:參照封裝要求,對多款底盤配置進行評估,然后通過多次 CAE 分析完成設計定型。正確的封裝意味著所有零部件都能配合運行而不受任何干擾,并且能夠正常裝配和拆卸。最優設計不僅需要結構牢固,還必需滿足裝配要求。從封裝角度考慮,每一個完整的 CAE 迭代都需要包含三個獨立的分析:彎曲剛度、扭轉剛度和模態。使用這一傳統方法必須執行三到四次完整的 CAE 迭代,而每次迭代往往需要兩到三周的時間。
團隊借助 COMSOL 多物理場仿真軟件將三個獨立的分析進行了整合,從而將完整的 CAE 迭代次數減少至一到兩次,由此節省了寶貴的時間。他們隨后又將基于鐵木辛柯梁理論(Timoshenkobeam theory)的一維梁模型(圖 5)封裝為底盤設計仿真 App。最終用戶無需了解底層數學模型,就能從仿真 App 的計算結果中受益。即便是包含大量不同橫截面和構件的復雜底盤設計,仿真也只需短短數秒即可完成。如圖 6 所示,梁分析為各類配置提供了快速而可靠的結果,并計算了扭轉剛度、彎曲剛度和位移。仿真 App 主要服務于負責底盤和穩定桿設計的驅動底盤(drive away chassis,簡稱 DAC)懸架團隊,支持通過輸入簡單的文本字段對不同的設計參數進行計算,無需為每個配置創建 CAD 模型,這種便捷性節省了 CAE 分析師和 DAC 懸架團隊的寶貴時間。
圖 5. 馬恒達公司內部門戶提供的汽車底盤仿真 App (名為 MathApps) 的用戶界面。
圖 6. 底盤設計 App 針對特定配置提供的仿真結果。
仿真 App 開拓未來設計道路
馬恒達開發的仿真App具有處理各種參數變化、物理場和邊界條件的強大能力。得益于此,設計人員在產品開發的早期階段便可以探索各種設計方案,完全擺脫了對CAE分析師的依賴。參數化研究的結果可以對設計進行指導,從而提升產品性能,并降低加工成本。
仿真 App 的開發融合了設計人員和 CAE 分析師的意見和反饋,并通過公司內部安裝的 COMSOL Server? 產品在馬恒達的各個團隊中進行部署。以前只能由 CAE 分析師經手的復雜設計配置,現在可以讓設計人員在簡單易用的平臺上隨時訪問。借助多物理場仿真和 App,馬恒達公司實現了強大的分析能力共享,他們期望在未來的工作中,將振動聲學和熱結構分析也納入仿真分析中。
本文內容來自《COMSOL News》2018,點擊“閱讀原文”,閱讀更多用戶成功案例。
-
發動機
+關注
關注
33文章
2474瀏覽量
69324 -
仿真
+關注
關注
50文章
4082瀏覽量
133613 -
APP
+關注
關注
33文章
1574瀏覽量
72490
原文標題:通過仿真優化轎車設計
文章出處:【微信號:COMSOL-China,微信公眾號:COMSOL】歡迎添加關注!文章轉載請注明出處。
發布評論請先 登錄
相關推薦
汽車電子電氣架構設計及優化措施
純電動汽車電機嘯叫噪聲解析
汽車領域多學科優化設計解決方案--Optimus
電動汽車無線充電優化匹配研究
優化電動汽車的結構性能
生產作業計劃仿真優化研究
混和動力汽車的操穩性及通過性仿真研究
新能源汽車控制器EMC/EMI仿真優化方法
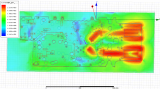
基于異步策略的Gazebo仿真優化方法
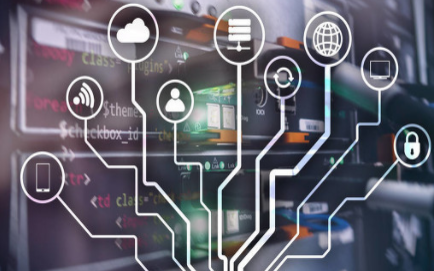
優化汽車應用的駕駛循環仿真
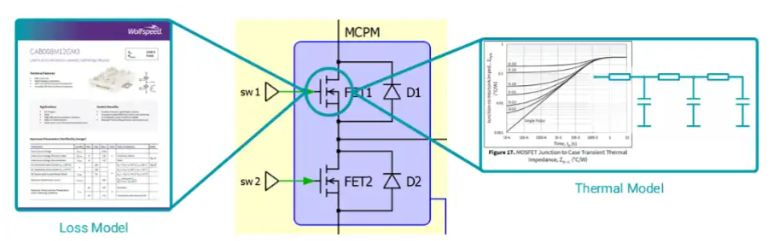
評論