一、概述
隨著電子信息產業的日新月異,微細間距器件發展起來,組裝密度越來越高,誕生了新型SMT、MCM技術,如圖1所示。
圖1 微電子學芯片封裝技術的發展
現在微電子器件中的焊點越來越小,但其所承載的力學、電學和熱力學負荷卻越來越重,對可靠性的要求也日益增高。電子封裝中廣泛采用的SMT封裝技術及新型的芯片尺寸封裝(CSP)、釬料球陣列(BGA)等封裝技術均要求通過焊點直接實現異材間電氣及剛性機械連接(主要承受剪切應變),它的質量與可靠性決定了電子產品的質量。
一個焊點的失效就有可能造成器件整體的失效,因此如何保證焊點的質量是一個重要問題。傳統SnPb釬料含Pb,而Pb及Pb化合物屬劇毒物質,長期使用含Pb釬料會給人類健康和生活環境帶來嚴重危害。目前電子行業對無Pb焊接的需求越來越迫切,已經對整個行業形成巨大沖擊。無Pb釬料已經逐步取代有Pb釬料,但無Pb化制程由于釬料的差異和焊接工藝參數的調整,必不可少地會給焊點可靠性帶來新的問題。因此,無Pb焊點的可靠性也越來越受到重視。
二、無Pb制程定義及系統考慮
(1)無Pb制程定義RoHS中規定禁止使用鉛(Pb)、汞(Hg)、鎘(Cd)、六價鉻(Cr6+)、多溴聯苯(PBB)、多溴二苯醚(PBDE)6種有害物質,實施日期是2006年7月1日。這意味著,從這天起,所有的EEE(電氣、電子設備),那些豁免的除外,一旦它們含有這6種禁用物質,就不能在歐盟市場上銷售。無一禁用物(如無Pb)的定義是什么?這6種禁用物質在任何一個EEE的均勻材質中所允許的最大濃度值(MCV)已在EU公報上公布,并在2005 年8月18日立法。
條款5(1)(a)規定,鉛、汞、六價鉻、多溴聯苯(PBB)、多溴二苯醚(PBDE)均勻材質的MCV 均為0.1wt%,鎘的MCV為0.01wt%。簡單地講,以無Pb為例,定義為任何一個EEE在所有的(單個的)均勻材質中,Pb含量小于0.1wt%。
(2)無Pb制程的系統考慮電子產品無Pb制程取代目前的有Pb工藝,已是大勢所趨。它正從研發走向產業化,從小批試產走向大規模量產,從消費類產品擴大到絕大多數的產品類型,兼容成為一個關鍵問題。在無Pb制程中,不管可靠性是否達到在苛刻環境中使用的電子產品的要求,都是必須關注的。苛刻環境的定義是:凡是必須長時間在溫度大幅度升高、持續承受很大負載、溫度劇烈變化、特別高的溫度、很強的機械撞擊或振動、腐蝕性等環境中工作的產品,或者同時要在上述幾種情況或者所有情況下使用的產品,均屬于“在苛刻環境下使用的電子產品”范疇。進一步講,由于電路設計方面的局限性,焊點兩邊的熱膨脹系數嚴重失配,也可以列入苛刻環境的范疇。從有Pb焊接過程到無Pb焊接的系統性考慮,包括設計、材料、工藝、質量,以及可靠性、設備、操作和商業化等多方面,而無Pb釬料的系統連接可靠性則是無Pb轉換的關鍵。無Pb焊接的系統考慮如圖2所示。
圖2 無Pb焊接的系統考慮
三、電子產品無Pb制程工藝可靠性理解
電子產品無Pb制程是怎樣影響到產品性能和工藝控制的,這是其執行的核心內容。從富Pb材料切換到無Pb材料時,失效模式和效果分析(FMEA)是有差異的。從機械角度看,典型的無Pb材料要比含Pb高的材料硬。硬度對插座設計、電氣接觸(阻抗和接觸電阻)及整個焊點均有影響。不僅無Pb合金具有較硬的特點,就連表面氧化物、助焊劑殘留物、合金污染物等殘留覆蓋物組合,也能在電氣接觸和接觸電阻上產生多種影響。因此,電子產品從富Pb向無Pb制程的轉換,在電氣或機械方面都不是一個普通的替換。當比較無Pb和富Pb釬料時,由于尺寸的變化,在倒裝芯片的釬料球和μBGA封裝間會產生持久性的變化。
Pb是比較軟的容易變形,因此無Pb制程的焊點硬度比有Pb的高,強度好些,變形也小些。但這一切并不等于無Pb制程焊點的可靠性好,由于無Pb釬料的潤濕性差,空洞、移位、立碑等焊接缺陷比較多。由于熔點高,如果助焊劑的活化溫度不能配合高熔點的較高溫度和較長時間的助焊劑浸潤區的話,就會使焊接面在高溫下重新氧化而不能發生浸潤和擴散效果,不能形成良好的界面合金層,其結果是導致焊點界面結合強度(抗拉強度)差而降低可靠性。
四、影響電子產品無Pb制程工藝可靠性的因素
無Pb焊點的可靠性問題主要來源于:
●焊點的剪切疲勞與蠕變裂紋;
●電遷移、釬料與基體金屬界面金屬間化合物形成裂紋;
●Sn晶須生長引起短路;
●電腐蝕和化學腐蝕問題。無Pb焊接工藝可靠性是一個非常復雜的工程問題,歸納起來主要取決于工藝可靠性設計、工藝操作規范及工藝管理等諸多因素,如圖3所示。
圖3 影響無Pb焊點工藝可靠性的因素
與傳統的有Pb工藝相比,無Pb化焊接由于釬料的差異和工藝參數的調整,必不可少地會給焊點可靠性帶來一定的影響。首先是無Pb釬料的熔點較高。傳統的Sn37Pb共晶釬料熔點是183℃,而共晶無Pb釬料(SAC387)的熔點為217℃,溫度曲線的提升隨之帶來的是釬料易氧化,金屬間化合物生長迅速等問題。其次,由于無Pb釬料不含Pb,潤濕性差,容易導致產品焊點的自校準能力、拉伸強度、剪切強度等不能滿足要求。以某OEM公司為例,原含Pb工藝焊點不合格率平均在50ppm左右,而無Pb制程由于釬料潤濕性差,不合格率上升至200~500ppm。
與傳統的含Pb工藝相同,影響無Pb工藝焊點可靠性的因素也可以大致分為下述幾個方面。
1.釬料合金的影響釬料合金的選擇極為重要。目前,大多采用SAC合金系列,液相溫度是217~227℃,這就要求再流焊具有較高的峰值溫度,如前所述會帶來釬料及導體材料(如Cu箔)易高溫氧化,金屬間化合物生長迅速等問題。因為在焊接過程中,熔融的釬料與焊接襯底接觸時,由于高溫在界面會形成一層金屬間化合物(IMC)。其形成不但受再流焊接溫度、時間的控制,而且在后期使用過程中其厚度還會隨時間而增加。
界面上的IMC是影響焊點可靠性的一個關鍵因素。過厚的IMC層的存在會導致焊點斷裂、韌性和抗低周期疲勞能力下降,從而導致焊點的可靠性降低。無Pb釬料中Sn含量都比SnPb釬料高,這更增大了焊點和基體金屬間界面上形成IMC的速率,導致焊點提前失效。
另外,由于無Pb釬料和傳統SnPb釬料成分不同,因而它們和焊盤材料,如Cu、Ni、Ag、Pd等的反應速率及反應產物也可能不同,焊點也會表現出不同的可靠性。同時釬料和助焊劑的兼容性也會對焊點的可靠性產生非常大的影響,有研究表明:釬料和助焊劑各成分之間不兼容會導致附著力減小。此外,由于熱膨脹系數(CTE)不匹配,又會加快釬料周期性的疲勞失效。
因此,要特別注意選擇兼容性優良的釬料和助焊劑,才能承受住無Pb再流焊時的高溫沖擊。
●目前有Pb釬料合金大都使用的是Sn37Pb,熔點為183℃。
●目前業界無Pb制程再流焊接中“主流”釬料合金是SAC,其中應用最廣的成分是SAC305和SAC387(共晶組分),前者熔化溫度范圍為217~220℃,后者為共晶組分,熔點為217℃,而波峰焊接則可能是SAC305或Sn0.7Cu(x)(熔點為227℃)。SAC合金和SnCu(x)合金擁有不同的可靠性特性。由上可知,無Pb共晶組分SAC387比有Pb共晶組分Sn37Pb合金的熔點要高出34℃。
顯然,從有Pb焊接轉變到無Pb焊接并不僅僅是單純的材料代換而已,它還帶來了許多可靠性方面的困擾。微電子領域使用的釬料有著很嚴格的性能要求,無Pb釬料(以SAC為例)也不例外,不僅包括電學和力學性能,還必須具有理想的熔融溫度。從制造工藝和可靠性兩方面考慮,表1列出了釬料合金的一些重要性能。表1 釬料合金的重要性能
2.元器件影響元器件可靠性的因素如下。
(1)高溫影響。某些元器件,如塑料封裝的元器件、電解電容器等,受高的焊接溫度的影響程度要超過其他因素。
(2)Sn晶須的影響。Sn晶須是長壽命的高端產品中精細間距元器件更加需要關注的另一個問題。無Pb釬料合金均屬高Sn合金,長Sn晶須的概率比SnPb高得多。通過限制Sn層厚度來限制晶須的最終長度并不實際。人們普遍相信添加3wt%或更多Pb可防止晶須的形成,并且這種現象很少在SnPb焊點上發生。雖然偶爾觀察到SnPb釬料中長出長達25~30μm的晶須,但可能是在大電流下電遷移效應導致的異常析出現象。
(3)應力的影響。SAC合金也會給元器件帶來更大的應力,使低k介電系數的元器件更易失效。
(4)焊端表面鍍層的影響。無Pb元器件焊端表面鍍層的種類很多,有鍍純Sn和SAC的,也有鍍SnCu、SnBi等合金的。鍍Sn的成本比較低,因此采用鍍Sn工藝比較多。但由于Sn表面容易氧化形成很薄的氧化層,加上電鍍后易產生應力形成Sn晶須。Sn晶須在窄間距的器件QFP等容易造成短路,影響可靠性。故對于低端產品及壽命要求小于5年的元器件可以鍍純Sn。而對于高可靠產品及壽命要求大于5年的元器件,則應先鍍一層厚度為1μm以上的Ni,然后再鍍2~3μm厚的Sn。
(5)零部件的供應質量問題。由于各部件均來自于不同廠商,因而部件質量難免參差不齊,如器件引腳可焊性不足等。由于以前的熱風整平(HASL)焊盤涂層工藝存在缺點,如今的OEM廠商應用較廣泛的包括有機可焊性保護層(OSP)等涂層工藝。
3.PCB
(1)基材某些PCB(特別是大型復雜的厚PCB)根據層壓材料的屬性,可能會由于無Pb焊接溫度較高而導致分層、層壓破裂、Cu裂縫、CAF(導電陽極絲)等失效故障率上升。它還取決于PCB表面涂層,例如釬料與Ni層(ENIG涂層)之間的接合要比釬料與Cu(如OSP和浸銀)之間的接合更易斷裂,特別是在機械撞擊下(如跌落測試中)尤為明顯。
(2)焊盤涂層表面處理的最主要作用就是確保金屬基底(通常是銅)的可焊性。由于以前的熱風整平(HASL)焊盤涂層工藝存在缺點,可替代的表面涂層包括:有機可焊性保護膜(OSP)、Ni/Au、Ni/Pd/Au、Im-Sn和Im-Ag等。其中Ni/Au涂層又有ENIG Ni/Au和EG Ni/Au兩種。無論選擇哪種表面處理,它都必須維持精確的信號完整性,確保在任何情況下信號完整性都不會下降。選擇正確的鍍層還需要考慮的問題包括:電磁兼容(EMI)、接觸電阻和焊點的強度。最后使用的表面處理要有利于控制電磁干擾。它還不能因為時間長而降低性能,否則在表面處理層/焊盤的連接部位會出現泄漏造成電磁干擾的問題。EG Ni/Au和ENIG Ni/Au都存在明顯的可靠性問題,SnPb焊點在EG Ni/Au焊盤上的接合強度在使用幾年后就可能大幅下降。由于無法對Au鍍層的厚度實施有效且一致的控制,因此,建議在SnPb焊接中不采用Ni/Au的焊盤。
(3)PCB厚度的影響相同封裝安裝到不同厚度的PCB上的溫度循環結果是:在使用的條件范圍內,較薄的PCB擁有較長的溫度循環壽命。事實上,厚PCB更難使得封裝的熱膨脹和收縮相一致,因此在焊點處導致了較大的熱應力。4)焊盤定義對焊點可靠性的影響相同封裝分別采用NSMD和SMD焊盤定義,如圖4所示。以純有Pb情況為例,將元器件連接到PCB上后,焊點的可靠性是不一樣的。在循環溫度范圍為-40~125℃/10min的條件下,其壽命F(t)的威布爾分布如圖5所示。
圖4
圖5 NSMD/SMD焊點
在高低溫溫度循環試驗中F(t)的威布爾分布圖NSMD結構比SMD結構擁有較長的溫度循環壽命。當采用NSMD結構時,焊接的連接力較大的原因是:焊盤的連接面積擴展到焊盤的側面了。
(5)單面焊接和雙面焊接存在的可靠性差異進行單面焊接和雙面焊接轉換安裝(如表2所示)的結果,以及隨后的溫度循環特性比較,如圖6、圖7所示。即封裝安裝在底部面上時,就相當于被同樣寬度大小的焊盤所替換,其溫度循環特性幾乎和單面焊接相同。表2 雙面焊接驗證
圖6 安裝形式Ⅰ~Ⅳ在溫度循環中的威布爾分布圖(以有Pb為例)
圖7 單面和雙面安裝在溫度循環試驗中的威布爾分布(以有Pb為例)
(6)元器件引腳電鍍和引腳材料的接合(1)引腳材料:Cu。焊盤類型為SMD,安裝傳統SnPb電鍍元器件引腳和無Pb的SnBi電鍍元器件,采用傳統Sn37Pb釬料或無Pb的SAC305釬料的焊點可靠性、溫度循環試驗的結果,如圖8所示。
圖8引腳材料為Cu的焊點溫度循環試驗的威布爾分布
無Pb產品和無Pb釬料的接合的溫度循環特性優于傳統工藝接合,并且傳統產品和無Pb釬料,以及無Pb產品和傳統釬料的接合都得到了較差的結果。(2)引腳材料:Fe-Ni。焊盤類型為SMD,安裝傳統SnPb電鍍元器件引腳和無Pb的SnBi電鍍元器件引腳,采用傳統Sn37Pb釬料和無Pb的SAC305釬料的可靠性、溫度循環試驗結果如圖9所示。
圖9 引腳材料為Fe-Ni的焊點溫度循環試驗的威布爾分布
無Pb元器件引腳和無Pb釬料的接合的溫度循環試驗特性優于傳統工藝接合,并且傳統元器件引腳和無Pb釬料,以及無Pb元器件引腳和傳統釬料的接合都得到了較差的結果。
5.工藝因素
1)工藝可靠性設計合適的PCBA組裝工藝可靠性設計,可從兩個方面來改善BGA、CSP等球柵陣列芯片焊點的可靠性,兩者結合起來可以很大程度地提高器件的可靠性。這些方法如下:
(1)選擇相近的熱膨脹系數(CTE)材料來減少整體熱膨脹的不匹配。
(2)通過控制合適的焊點高度(器件的離板高度)來增加焊接層的一致性,以此來減少整體熱膨脹的不匹配。另外,以高可靠性為目的的可靠性設計規范還包括:
(3)通過在元器件和PCB基板之間添加合適的底部填充膠進行機械連接,從而消除整體熱膨脹不匹配的影響。
(4)選擇一種軟的晶片黏結層來降低晶片熱膨脹系數(2.7~2.8ppm/℃)在整體熱膨脹不匹配和局部熱膨脹不匹配的影響。選擇特定范圍熱膨脹系數包括材料的選擇或多層板和元器件之間材料的組合,來得到最佳的熱膨脹系數。當多層板有較大的熱膨脹系數時,有源器件最佳的熱膨脹系數約為1~3ppm/℃(與功率的耗散有關),無源元件的熱膨脹系數為0ppm/℃。當然,一個電子組裝中有大批不同的元器件,要想實現熱膨脹系數全部最優化是不可能的,這會給元器件帶來極大的可靠性威脅。
對一些有密封性要求的軍事應用產品,就需選用陶瓷元器件。選擇特定范圍熱膨脹系數,就意味著熱膨脹系數受到限制的多層板材料只能在Kevlar和石墨纖維(一種質地牢固重量輕的合成纖維),或者在銅-因瓦合金-銅和銅-鉬-銅之間選擇。這些解決方法對絕大多數商用產品來說顯得太昂貴了,商用產品的多層板大多選用玻璃-環氧樹脂或玻璃-聚酰亞胺材料。選擇特定范圍熱膨脹系數的材料必須避免選取一些較大的元器件,如陶瓷元件(CGAs、MCMs)、引腳數為42的塑料封裝(TSOPs、SOTs)或者是與晶片采用剛性連接的塑料封裝(PBGAs)。對無Pb焊接接合部來說,要增加其相容性就意味著要增加焊點的高度或轉向有Pb焊接接合部技術。因為有Pb焊接接合部增加了Pb的相容性,那就意味著要由元器件供應商轉向更能提高Pb相容性的幾何形狀或轉向細間距技術。可靠性設計過程不僅要強調器件失效的物理原因,還不能忽視失效的數據統計分布。
這個過程可能包含以下一些步驟:
① 確定可靠性要求——希望的設計壽命及在設計壽命結束之后的可接受的失效概率;
② 確定負載條件——由于功率耗散原因,要考慮使用環境(如IPC-SM-785)和熱梯度,這些參數可能會發生變化,并產生大量的小型循環;
③ 確定/選擇組裝的結構——元器件和基板的選擇,材料特性(如熱膨脹系數)及焊接接合部的幾何形狀。
2)SMT工藝流程因素考慮到無Pb釬料與傳統PbSn釬料的差異,就需要從工藝控制上來彌補其不足,以達到產品組裝的要求。主要因素有:
(1)焊膏印刷定位精度提高,以彌補無Pb焊膏自校準能力差的不足。
(2)工藝窗口狹窄就要求設備的控溫精度更高,并能具有氮氣氣氛控制,以改善浸潤性能;同時要根據組裝產品的不同特點合理設置再流溫度曲線。
(3)再流焊接溫度曲線一般由升溫預熱、均熱、再流及冷卻區組成。
●典型升溫速率為0.5~1.5℃,一般不超過2℃。
●峰值溫度推薦值為235~245℃,范圍為230~260℃,目標為240~245℃。
●停留在液相溫度以上時間為45~75s,允許為30~90s,目標為45~60s。
●再流焊溫度曲線總長度:從環境溫度升至峰值溫度的時間為3~4min。
●進入液相溫度再流區前要完成的功能是:使焊膏中的有機成分及水汽充分揮發;使被焊元器件預熱,大、小元器件溫度均衡;焊膏中的助焊劑充分發揮活性以清潔被焊面。
●具體再流焊溫度曲線的設置,要根據焊膏的特性,如熔點或液相線溫度、助焊劑活性對溫度要求、組裝產品的特點來決定。還應關注:釬料儲存溫度不當,焊盤釬料不足。此處特別需注意的一點是含Bi無Pb釬料的使用問題,由于含Bi釬料與SnPb涂層的器件接觸時,再流焊后會生成SnPbBi共晶合金,熔點只有99.6℃,極易導致開裂的發生。
因此,對含Bi無Pb釬料的使用,需注意器件涂層是否為SnPb涂層。3)有Pb或無Pb狀態下的爐溫曲線參數比較在純有Pb或純無Pb再流焊接的情況下,因為不存在焊端鍍層材料、BGA/CSP釬料球和焊膏材料之間的匹配和兼容問題,所以再流焊接爐溫參數的設置,基本都是有成熟的經驗數據作為借鑒,如表3所示。表3 有Pb、無Pb再流焊接溫度曲線的工藝參考數據和比較
●另外由于熔點高,助焊劑的活化溫度不能匹配高熔點;
●助焊劑浸潤區的溫度高、時間長,會使焊接面在高溫下重新氧化而不能發生浸潤和擴散,不能形成良好的界面合金層,結果導致焊點界面接合強度(抗拉強度)差而降低可靠性。
6.環境影響因素
1)機械負荷條件焊點上的機械應力來源于對插件板上施加的外力。在外加機械負荷的情況下,尤其是系統機械沖擊引起的負荷,釬料的蠕變應力總是比較大的,原因是這種負荷對焊點施加的變形速率比較大。因此,即使是足以承受熱循環的金屬間化合物結構,也會在剪力或拉力測試期間最終成為最脆弱的連接點。SAC合金的高應力率靈敏度,要求更加注意無Pb焊接界面在機械撞擊下的可靠性(如跌落、彎曲等),在高應力變化速率下,應力過大更易導致焊接互連斷裂。2)熱機械負荷條件焊接結構內部不匹配的熱膨脹。在足夠高的應力下,釬料的蠕變特性有助于限制焊點內的應力。即使是一般的熱循環,通常也要求若干焊點能經受得住在每次熱循環中引起蠕變的負荷。因此,焊盤上金屬間化合物的結構必須經受住釬料蠕變帶來的應力。
-
制程工藝
+關注
關注
0文章
44瀏覽量
9455
發布評論請先 登錄
相關推薦
SMT貼片技術的重要性:如何影響電子產品的制造與品質
電子產品結構與導熱材料解決方案
三防測試:揭秘電子產品的可靠性檢測
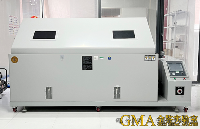
PCB高可靠性化要求與發展——PCB高可靠性的影響因素(上)
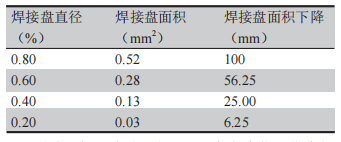
電子產品環境模擬試驗有哪些?
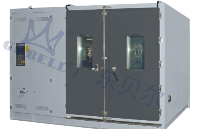
評論