本文對軟包裝鋰離子電池生產過程中的脹氣類型及原因進行了分析,并從材料體系優化及工藝控制等方面給出了抑制產氣發生的相關措施,對軟包裝鋰離子電池的制程優化和產品品質提升具有重要意義。
電池的能量密度要求不斷提高,電池的尺寸空間也越來越小,軟包裝鋰離子電池稍有氣脹現象就會影響用電器使用,降低電池性能,嚴重時將會撐破包裝鋁箔,造成漏液腐蝕危險。
因此了解電池脹氣產生的原因掌握抑制脹氣方法,對保證電池性能,提高其循環壽命及安全性能有重要意義。本文結合生產實際,分析氣脹的類型和產生的可能原因,并提出解決方案,供大家參考。
一、氣體產生的類型
軟包裝鋰離子電池氣體的產生分為正常產氣和異常產氣兩種。正常產氣是指在電芯生產工藝過程中的化成工序,SEI膜的形成過程中伴隨產生的,常稱為化成產氣。此種氣體一般可暫時存放于氣袋中,并于后續工序中排出,對電芯不產生明顯影響。
異常產氣是指,當氣袋切除,封裝完成后,由于電池內部發生異常造成氣體量過多,此種情況下氣體不能排出,引起電芯鼓脹,影響用電器使用,且會對電芯造成性能惡化。當內部壓力過大時,容易撐開包裝鋁箔,造成漏液、腐蝕等嚴重損害。因此了解電芯整個產氣過程,防止異常產氣發生是軟包裝鋰離子電池生產的關鍵。
1 化成產氣
化成產氣是指在電芯制造工藝過程的化成工序,也即電池的首次充電過程中,電解液在電極表面發生了氧化、還原反應,形成固體電解質膜(SEI膜)時伴隨著產氣;中國電子科技集團公司第十八研究所的陳益奎等研究了正極、負極產氣量對比與氣體成分分析,得出電池出化成階段產氣主要集中在電池負極。廈大寶龍電池研究所的黃麗等人詳細研究了不同化成電壓下,所產生的氣體種類和數量。
研究結果表明,在2.5V以下,產氣主要為H2和CO2;2.5V以后,EC少量開始分解,產物主要為C2H4;3V后,電解液中DMC和EMC開始分解,產氣除了C2H4外,還包含CH4和C2H6等烷烴;電壓超過3.8V,EC分解的產物C2H4基本消失。電壓在3.0~3.5V,化成過程產氣量最大,表明在3.5V時,為SEI膜的主要成膜區。
SEI膜離子導通電子不導通,在結構上由兩層組成,內層為致密穩定的無機層,外層為多孔疏松的有機層,厚度在2nm到幾十納米之間,外層有機產物層,具有一定的柔韌性,可以提高整個膜層的機械強度和完整性,有效阻隔溶劑分子在電極表面持續的還原反應,因此,3.5V以后由于SEI膜的阻隔作用,產氣基本完成,產氣量迅速下降。在SEI膜形成過程中EC的分解包括一電子反應和二電子反應兩種:
其中一電子反應形成烷基碳酸鋰并伴隨大量乙烯氣體產生,如下(1)和(2)所示;
二電子反應主要形成碳酸鋰和CO氣體,如反應(3)~(5)所示:
較好的電解液和合適的材料匹配可以產生優良穩定的SEI膜,不僅能有效阻隔電解液分解,提高首次效率,而且后續因SEI的溶解和再生所產生的氣體量少,因此有效選擇材料和電解液體系可以降低化成產氣量,提高電池綜合性能。
2 異常產氣
在軟包電池生產工藝過程中,有很多因素可以導致異常產氣,其中分為幾大類:一是電芯本身成膜不穩定,在后續的循環過程中,負極表面的SEI膜可能脫落或者變疏松,并進行SEI膜重構,伴隨氣體產生;二是電芯內部水含量超標導致;三是電池內短路導致異常產氣;四是高溫存儲過程產氣;五是過充過放產氣。
其中,成膜的致密和穩定是電芯性能得以保障的前提,水含量超標和電池內短路是生產過程中經常出現的問題。下面將對這幾種情況進行簡要分析。
二、 異常產氣原因分析
1 水含量異常脹氣
由于整個電池體系對水分的敏感性,雖有大量研究認為痕量水分的存在產生的LiF使得SEI膜性能更穩定,但當有過量水分的存在時,不但消耗鋰鹽量增加,降低電池性能,而且還會伴隨大量氣體產生,使電池發生氣脹,導致電池失效,當負極有鋰析出時遇到水會發生劇烈反應產生熱量引發更為嚴重的安全問題。所以,水分控制是鋰離子電池生產的前提,也是軟包裝電池在生產過程中需要嚴格控制的工藝參數。
水分超標電芯的表現集中有兩點:一是氣體成分中氫氣含量明顯增大,二是從化成容量來看,脹氣電芯比正常電芯容量更小。這是由于水分在電芯內部會發生一系列的反應,造成大量副反應氣體產生,引起脹氣。在整個反應過程中首先是水分本身在充電時被電解,產生氫氣,如反應(15)所示;其次是水與電解液中鋰鹽發生反應,生成氟化氫氣體,此種氣體還會腐蝕鋁箔。
從表1的氣體成分分析對比可以很明顯地看出,水含量異常導致的脹氣電芯中氫氣的含量明顯增多,放置時產生的HF極易與鋁箔發生腐蝕反應,因此氣體成分中未檢測到HF的存在。
表1 正常電芯和脹氣電芯氣體成分分析
水含量的引入使得電池內部發生副反應,造成界面破壞,化成過程中極化增大,很容易達到充電電位,使得充電時間普遍比正常電芯小,因此充電容量比正常電芯更小(圖1)。
圖1 脹氣電芯與正常電芯化成充電容量對比
電芯內部水含量超標,引發原因有多種,但大致可分為兩大類:一種是由于封裝不良,后續空氣中的水分進入電芯內部導致;另一種是生產工藝過程中水分控制不良導致,如膜片未烘干即進行注電解液操作;干燥房水含量超標;電解液在使用過程中引入了水分等。如圖2所示,隨著時間增加,裸電芯內部水含量不斷增加,真空烘烤后的裸電芯應及時進行注液封口,防止隨著放置時間的增長水分又重新進入膜片,導致后續的脹氣發生。
圖2 真空烘烤后裸電芯隨時間增加水含量變化曲線
2 內短路脹氣
電池在生產過程中,當有內短路點出現時,局部溫度急劇升高,導致電解液分解,對此種脹氣電池的氣體成分進行分析發現CO2含量大大增加,這是由于電解液在高溫和痕量水的存在下與LiPF6的分解產物PF5發生反應(20)和(21),使得CO2量明顯增加,發生氣脹。
由于內短路發生時,溫度可以達到200℃以上,并使隔膜燒灼碳化,此種電芯拆解時一般可以發現燒灼的短路點,且在高溫下正極Li0.5CoO2發生分解產生的氧氣加速了電解液中主要溶劑EC的分解,如下面反應所示,使得氣體鼓脹一般較為嚴重(表 2)。
表 2 正常電芯和脹氣電芯的氣體成分對比
3 高溫存儲及過充過放脹氣
在高溫存儲及過充過放過程中,LiCoO2處于亞穩狀態,極不穩定,會發生如下分解反應,如(22)~(24)所示:
此外,當SEI膜穩定性較低時,膜外層與電解液接觸的有機層會隨著溫度的升高發生溶解,如(CH2OCO2Li)2作為SEI膜烷基酯鋰層的主要成分,很不穩定,易發生如(25)的分解反應,產生氣體,電芯發生鼓脹;
三、 抑制異常產氣的措施
在正常電壓范圍內,產氣量較少,而且大多為碳氫化合物,當有異常產氣發生時,會產生大量氣體,破壞電極界面結構,導致電解液分解失效,嚴重時沖破封裝區造成漏液,腐蝕危險。
抑制異常產氣需要從材料設計和制造工藝兩方面著手。
首先要設計優化材料及電解液體系,保證形成致密穩定的SEI膜,提高正極材料的穩定性,抑制異常產氣的發生。針對電解液的處理常常采用添加少量的成膜添加劑的方法使SEI膜更均勻、致密,減少電池在使用過程中的SEI膜脫落和再生過程產氣導致電池鼓脹。
相關研究已有報道并在實際中得到應用,如哈爾濱理工大學的成夙等報道,使用成膜添加劑VC可以減少電池氣脹現象。但研究多集中在單組分添加劑上,效果有限。華東理工大學的曹長河等人,采用VC與PS復合作為新型電解液成膜添加劑,取得了很好的效果,電池在高溫擱置和循環過程中產氣明顯減少。
研究表明,EC、VC形成的SEI膜組分為線性烷基碳酸鋰,高溫下附在LiC的烷基碳酸鋰不穩定,分解生成氣體(如CO2等)而產生電池鼓脹。而PS形成的SEI膜為烷基磺酸鋰,雖膜有缺陷,但存在著一定的二維結構,附在LiC高溫下仍較穩定。當VC和PS復合使用時,在電壓較低時PS在負極表面形成有缺陷的二維結構,隨著電壓的升高VC在負極表面又形成線性結構的烷基碳酸鋰,烷基碳酸鋰填充于二維結構的缺陷中,形成穩定附在LiC具有網絡結構的SEI膜。此種結構的SEI膜大大提高了其穩定性,可以有效抑制由于膜分解導致的產氣。
此外由于正極鈷酸鋰材料與電解液的相互作用,使其分解產物會催化電解液中溶劑分解,所以對于正極材料進行表面包覆,不但可以增加材料的結構穩定性,還可以減少正極與電解液的接觸,降低活性正極催化分解所產生的氣體。因此,正極材料顆粒表面形成穩定完整的包覆層也是目前的一大發展方向。
其次要嚴格控制制造工藝過程參數,保證封裝可靠性,防止電池內部水分過量引起的脹氣,控制方法如下:
(1) 電芯卷繞完成后干燥充分,防止膜片中水分含量超標;
(2) 嚴格控制真空烘烤后電芯到注液時間及干燥房濕度;
(3) 保證注液手套箱密封性;
(4) 控制電解液中水分和游離酸含量;
(5)規范電解液存儲環境及密封條件,防止電解液在使用及存放過程中進入過量水分;
(6) 采用閉口加壓化成或者外置氣囊化成后抽真空封口排氣;
(7) 采用多步化成和高溫擱置工藝,保證產氣完全;
(8) 提高封裝可靠性。
四、 總結
脹氣的產生主要有正常化成產氣和異常產氣,要想抑制電池后期的異常產氣,需要從材料設計優化和工藝控制兩方面著手;選用具有穩定完整包覆層的正極材料,阻隔電解液與正極反應分解,匹配具有成膜添加劑的電解液,有效保證SEI膜的穩定性是抑制產氣發生的前提,工藝過程中要保證封裝可靠性,加強控制水及氧氣等體系敏感物質進入電池內部是有效解決電池脹氣的途徑。
-
鋰電池
+關注
關注
260文章
8108瀏覽量
170139 -
軟包
+關注
關注
0文章
2瀏覽量
1021
原文標題:精品收藏|理論結合實際,軟包裝鋰電池脹氣問題!
文章出處:【微信號:Recycle-Li-Battery,微信公眾號:鋰電聯盟會長】歡迎添加關注!文章轉載請注明出處。
發布評論請先 登錄
相關推薦
鋰電池脹氣是否與保護板有關,并如何印證
鋰電池放電均衡
動力型鋰電池與普通鋰電池的差別
【轉】鋰電池長期充滿電存放有什么危害
【轉】鋰電池經常滿電存放有什么危害?
鋰電池VS聚合物鋰電池,誰才是未來的主角?
本公司大量回收汽車退役底盤電池包,電動車鋰電池,庫存B品鋰電池,新能源汽車鋰電池時空模組電池包
本公司大量回收汽車退役底盤電池包,回收電動車鋰電池,回收庫存B品鋰電池,回收新能源汽車鋰電池
回收鋰電池,回收動力電池,回收軟包電池,回收動力電池模組,回收圓柱電池,鋰電池回收,圓柱電池回收
什么叫軟包鋰電池
軟包鋰電池脹氣怎么辦_軟包鋰電池脹氣還能用嗎
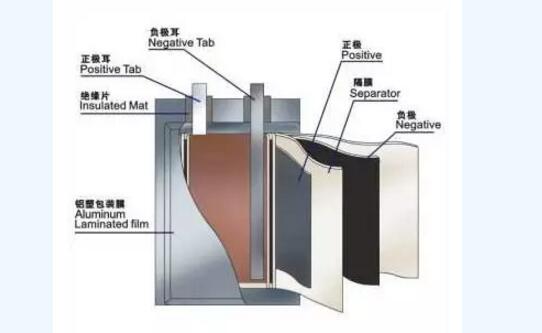
評論